www.ptreview.co.uk
08
'25
Written on Modified on
Yamaha Drives Re-engineering of Industrial Processes with Flexible Robotics Solutions
Industrial robots offer a flexible, fast, and affordable solution for automating manufacturing and packaging processes, supported with supplier expertise and simulation tools to select the best suited equipment and optimize processes and workflow.
www.yamaha-motor.com
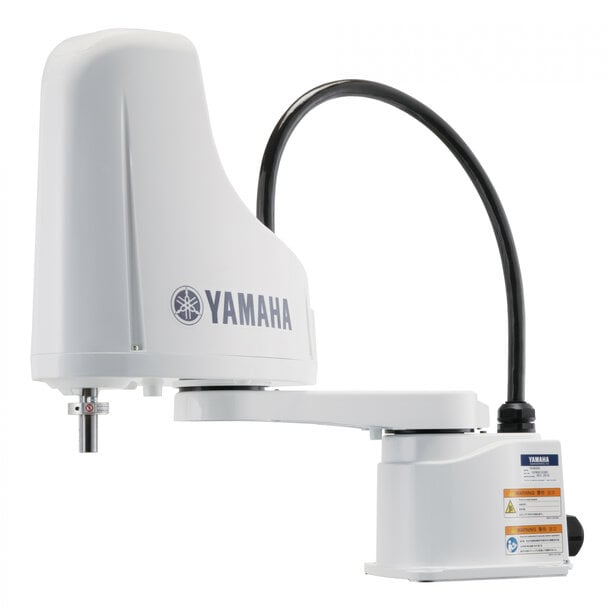
SCARA robots offer a fast and affordable solution for moving and placing objects with high accuracy
The business of making and selling is constantly evolving. Factory operators must respond to multiple forces for change; in markets, among competitors, from legislation, and the potential for disruptors to enter the competitive landscape. In the perpetual search for improvements, automation is a powerful tool that also demands significant financial investment and commitment of time and resources. Hence, planning properly is vital and the decision making must also recognise that the chosen automation, when installed, becomes part of the changing scene where flexibility is essential.
Flexible Automation
Robots have been widely regarded as a technology that can take over labour intensive manual tasks, but they can also offer a flexible, compact, and reprogrammable alternative to conventional factory automation. Machines in established formats, such as SCARA and cartesian robots, are available in small sizes, with arm length from over one metre down to a few centimetres. They can be rated for carrying loads from as much as 40-50kg down to less than 1kg and the fastest SCARA machines have cycle time below one second. The broad choice of different types and sizes gives factory planners many options when seeking a suitable solution. They can begin by changing one process that may be causing a bottleneck, or change an entire assembly line that may involve any combination of manual work and conventional automation.
When beginning to evaluate robot-based automation, it is important to identify the locations the new machines can be deployed most effectively, for the greatest improvement. Starting with a small-scale implementation, migrating just one or a few processes to a robot-based implementation, is often advised. By starting small, a functioning solution can be realised relatively quickly and the project can highlight key implementation challenges that show where extra knowledge may be needed to accomplish subsequent projects. The experience gained can inform these activities as automation is expanded to encompass other processes in the production line and across the factory floor.
Since speed, accuracy, strength, and endurance are major advantages of robots, in addition to their programmable flexibility, introducing them in industrial processes can take advantage of one or a combination of these attributes. Their lifting capabilities are one example. Some industrial products, such as EV battery modules, can weigh between 30-50 kg. On the other hand, containers filled with liquids such as engineering oils or cleaning fluids can weigh just a few kilograms. Introducing a high-speed SCARA robot at the end of the line can improve productivity by taking over the repeated lifting and moving, which can eventually become tiring for any human operator over the course of a shift. Fatigue brings an increasing probability of injury. Moreover, the robot is capable of placing the item accurately in a required position. A human worker’s accuracy will deteriorate over time, particularly if the items weigh a few kilograms or more.
Implementation
Yamaha Robotics has demonstrated solutions that implement end-of-line processes using robots, including a test and assembly station for electric vehicle batteries, at recent industry exhibitions in Europe. This battery module handler illustrated heavy lifting, rapid positioning, and accurate placement of 35kg lithium-ion modules in a test fixture for electrical testing, followed by stacking the modules in battery packs.
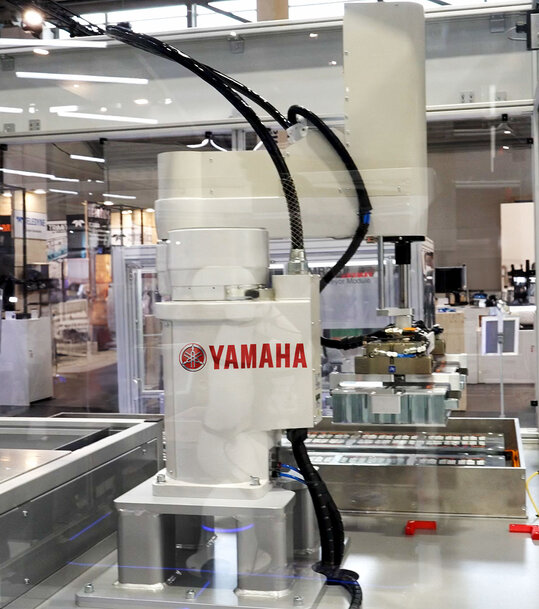
End-of-line EV battery-module handling demonstrated heavy lifting, high speed and accurate placement with a SCARA robot
Accuracy is another strength of SCARA robots and smaller machines can take over precision assembly tasks such as press-fitting components or driving screws. Pneumatic screwdrivers are widely used in assembly areas, to help operators work quickly and ensure the correct torque is applied. However, errors can occur. One example is where screws are required to be inserted in deep holes. Some can be missed as operators cannot see whether a screw has been inserted. Automating the screwdriving processes provides certainty that every item is inserted and tightened satisfactorily.
A robot installed at a specific workstation in the production line can take over a task like screwdriving and significantly improve overall production yield and quality assurance. An articulated robot, or cobot, can perform the task in much the same way as a human operator, ensuring greater repeatability. Alternatively, a SCARA robot, integrated together with a suitable screw feeder in a compact work cell, can deliver the superior repeatability as well as an extremely fast cycle time. The smooth motion control that characterises SCARA robots also makes these machines ideal for dispensing air-curable adhesives, gasketing materials, or sealers.
Another popular approach is to deploy robots in offline processes, such as testing electronic assemblies and personalising or individually configuring products before storing in inventory or shipping to a customer. In 2024, Yamaha demonstrated a solution that configures electrical connectors in accordance with instructions in a network file. The cell contains a SCARA robot that selects and loads the appropriate punching tool, with integrated vision to verify the correct pins have been punched and that there are no burrs. The process is guided by barcode to prevent errors and can handle different connectors in the same operation. Automated loading and unloading of electronic assemblies into a test fixture for in-circuit and functional testing was also demonstrated, based on a cartesian robot to ensure precise positioning of the assembly for electrical continuity.
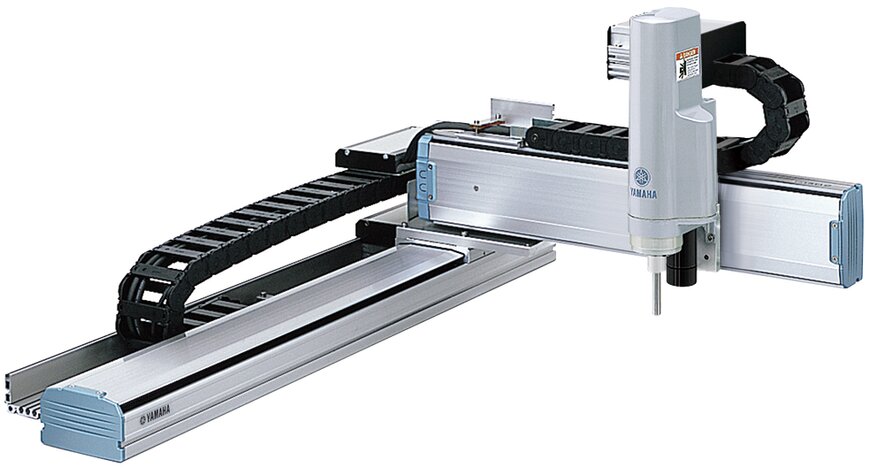
Cartesian robots can move objects and carry out processes with high accuracy
Selection and Optimisation
Creating a turnkey automation solution demands a combination of skills to bring together robots and software, application-specific tooling, and system integration. To ensure the robots can operate as efficiently as possible, the workflow and physical layout of the plant may need to be adapted.
Suitable simulation tools can provide valuable help to plan the production line, select the most appropriate types of automation for each process, and optimise the cycle time and throughput. By providing tools to create digital models of production lines, simulation software helps visualise layouts and workflows before physical implementation, as well as helping to pinpoint any bottlenecks or other inefficiencies in the system by simulating the flow of materials and processes and the interactions between robots, other automation, and people throughout the factory area. Simulating with tools such as the Robot Simulator in Yamaha RCX Studio permits experimenting with different configurations, equipment placements, and workflows. This enables project teams to find the most efficient setup before committing to hardware or making any physical changes in the factory.
Working with appointed sales agents and system integration partners, Yamaha continuously works on developing robot cells for specific manufacturing challenges. Drawing on these experiences can help expedite solutions to commonly encountered issues
Conclusion
Automating with robots can deliver an effective solution to enhance manufacturing productivity, while ensuring flexibility to adapt to changes in production requirements or product design features. Whether deployed inline, or in standalone processes performed offline, robots can be introduced selectively to prove the approach and build experience before scaling up to automate an entire sequence from end to end.
Simulation is a powerful tool that can augment careful study into optimising processes, the positions of robots in the line, and the cycle time, to achieve the highest possible equipment utilisation. The skills and knowledge of external organisations, including the robot supplier and system integrator are essential to realise an effective and optimised solution.
www.yamaha-motor-im.com
The business of making and selling is constantly evolving. Factory operators must respond to multiple forces for change; in markets, among competitors, from legislation, and the potential for disruptors to enter the competitive landscape. In the perpetual search for improvements, automation is a powerful tool that also demands significant financial investment and commitment of time and resources. Hence, planning properly is vital and the decision making must also recognise that the chosen automation, when installed, becomes part of the changing scene where flexibility is essential.
Flexible Automation
Robots have been widely regarded as a technology that can take over labour intensive manual tasks, but they can also offer a flexible, compact, and reprogrammable alternative to conventional factory automation. Machines in established formats, such as SCARA and cartesian robots, are available in small sizes, with arm length from over one metre down to a few centimetres. They can be rated for carrying loads from as much as 40-50kg down to less than 1kg and the fastest SCARA machines have cycle time below one second. The broad choice of different types and sizes gives factory planners many options when seeking a suitable solution. They can begin by changing one process that may be causing a bottleneck, or change an entire assembly line that may involve any combination of manual work and conventional automation.
When beginning to evaluate robot-based automation, it is important to identify the locations the new machines can be deployed most effectively, for the greatest improvement. Starting with a small-scale implementation, migrating just one or a few processes to a robot-based implementation, is often advised. By starting small, a functioning solution can be realised relatively quickly and the project can highlight key implementation challenges that show where extra knowledge may be needed to accomplish subsequent projects. The experience gained can inform these activities as automation is expanded to encompass other processes in the production line and across the factory floor.
Since speed, accuracy, strength, and endurance are major advantages of robots, in addition to their programmable flexibility, introducing them in industrial processes can take advantage of one or a combination of these attributes. Their lifting capabilities are one example. Some industrial products, such as EV battery modules, can weigh between 30-50 kg. On the other hand, containers filled with liquids such as engineering oils or cleaning fluids can weigh just a few kilograms. Introducing a high-speed SCARA robot at the end of the line can improve productivity by taking over the repeated lifting and moving, which can eventually become tiring for any human operator over the course of a shift. Fatigue brings an increasing probability of injury. Moreover, the robot is capable of placing the item accurately in a required position. A human worker’s accuracy will deteriorate over time, particularly if the items weigh a few kilograms or more.
Implementation
Yamaha Robotics has demonstrated solutions that implement end-of-line processes using robots, including a test and assembly station for electric vehicle batteries, at recent industry exhibitions in Europe. This battery module handler illustrated heavy lifting, rapid positioning, and accurate placement of 35kg lithium-ion modules in a test fixture for electrical testing, followed by stacking the modules in battery packs.
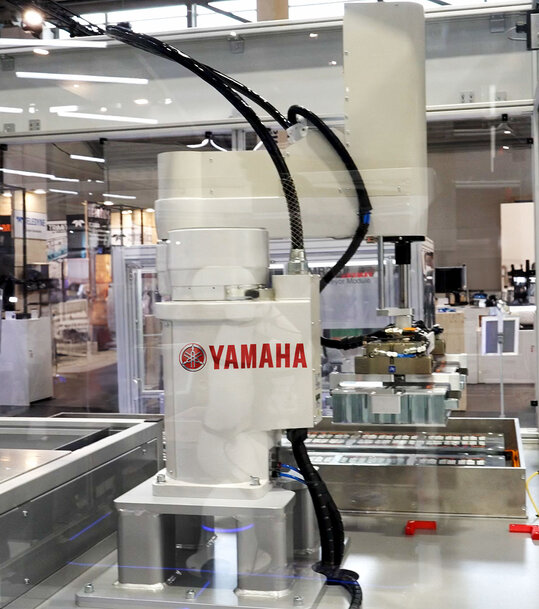
End-of-line EV battery-module handling demonstrated heavy lifting, high speed and accurate placement with a SCARA robot
Accuracy is another strength of SCARA robots and smaller machines can take over precision assembly tasks such as press-fitting components or driving screws. Pneumatic screwdrivers are widely used in assembly areas, to help operators work quickly and ensure the correct torque is applied. However, errors can occur. One example is where screws are required to be inserted in deep holes. Some can be missed as operators cannot see whether a screw has been inserted. Automating the screwdriving processes provides certainty that every item is inserted and tightened satisfactorily.
A robot installed at a specific workstation in the production line can take over a task like screwdriving and significantly improve overall production yield and quality assurance. An articulated robot, or cobot, can perform the task in much the same way as a human operator, ensuring greater repeatability. Alternatively, a SCARA robot, integrated together with a suitable screw feeder in a compact work cell, can deliver the superior repeatability as well as an extremely fast cycle time. The smooth motion control that characterises SCARA robots also makes these machines ideal for dispensing air-curable adhesives, gasketing materials, or sealers.
Another popular approach is to deploy robots in offline processes, such as testing electronic assemblies and personalising or individually configuring products before storing in inventory or shipping to a customer. In 2024, Yamaha demonstrated a solution that configures electrical connectors in accordance with instructions in a network file. The cell contains a SCARA robot that selects and loads the appropriate punching tool, with integrated vision to verify the correct pins have been punched and that there are no burrs. The process is guided by barcode to prevent errors and can handle different connectors in the same operation. Automated loading and unloading of electronic assemblies into a test fixture for in-circuit and functional testing was also demonstrated, based on a cartesian robot to ensure precise positioning of the assembly for electrical continuity.
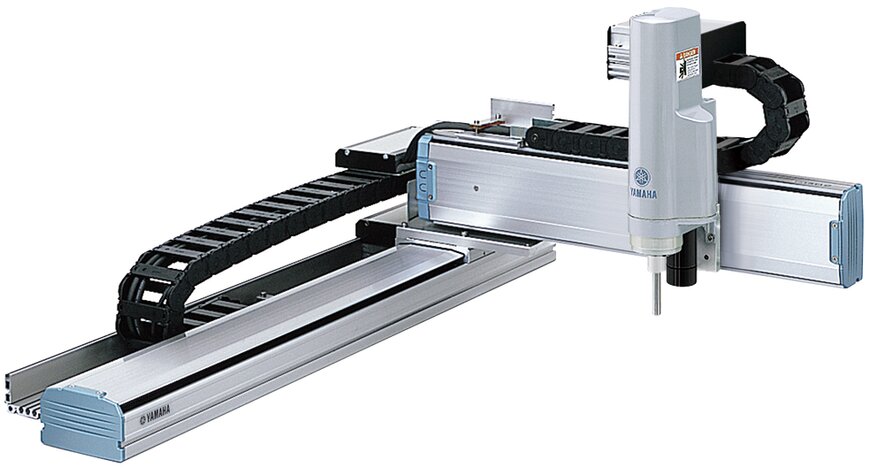
Cartesian robots can move objects and carry out processes with high accuracy
Selection and Optimisation
Creating a turnkey automation solution demands a combination of skills to bring together robots and software, application-specific tooling, and system integration. To ensure the robots can operate as efficiently as possible, the workflow and physical layout of the plant may need to be adapted.
Suitable simulation tools can provide valuable help to plan the production line, select the most appropriate types of automation for each process, and optimise the cycle time and throughput. By providing tools to create digital models of production lines, simulation software helps visualise layouts and workflows before physical implementation, as well as helping to pinpoint any bottlenecks or other inefficiencies in the system by simulating the flow of materials and processes and the interactions between robots, other automation, and people throughout the factory area. Simulating with tools such as the Robot Simulator in Yamaha RCX Studio permits experimenting with different configurations, equipment placements, and workflows. This enables project teams to find the most efficient setup before committing to hardware or making any physical changes in the factory.
Working with appointed sales agents and system integration partners, Yamaha continuously works on developing robot cells for specific manufacturing challenges. Drawing on these experiences can help expedite solutions to commonly encountered issues
Conclusion
Automating with robots can deliver an effective solution to enhance manufacturing productivity, while ensuring flexibility to adapt to changes in production requirements or product design features. Whether deployed inline, or in standalone processes performed offline, robots can be introduced selectively to prove the approach and build experience before scaling up to automate an entire sequence from end to end.
Simulation is a powerful tool that can augment careful study into optimising processes, the positions of robots in the line, and the cycle time, to achieve the highest possible equipment utilisation. The skills and knowledge of external organisations, including the robot supplier and system integrator are essential to realise an effective and optimised solution.
www.yamaha-motor-im.com