Automatization in the Food Industry: An answer to labour shortage?
The food industry is a big business. However, the lack of staff availability makes it next to impossible to take advantage of the opportunities that exist. There are even companies with orders and potential orders sitting on the table, as well as available factory space for additional lines and/or equipment - By K.A. Gerardino.
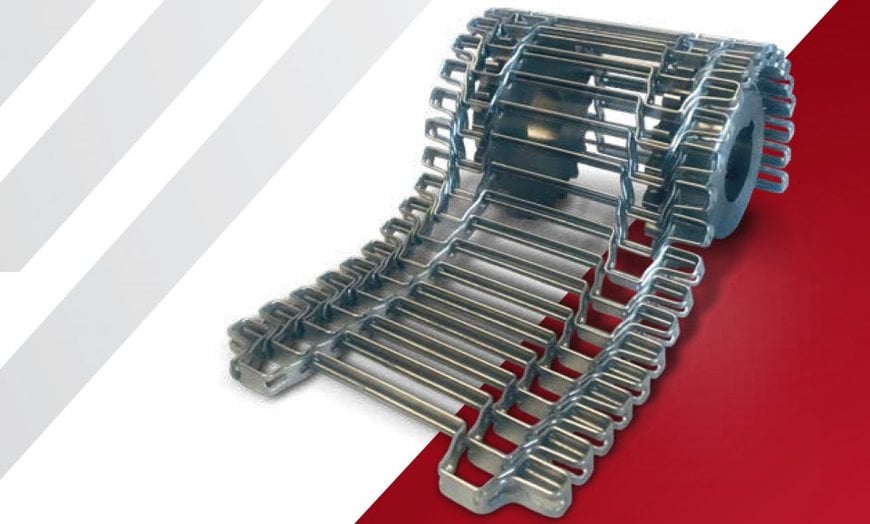
Although this is nothing new in the food business, it has become even more critical because of the present economic condition, the COVID-19 pandemic, and fluctuating prices of raw materials. Insufficient labour supply not only hinders food manufacturing companies’ production and operation, but affects the high-quality development.
To further add to the complexity, food manufacturing is not slowing down. The state of skilled labour has been below equilibrium for some time. As the previous generation of skilled laborers retires, the next wave of labourers entering the workforce is not nearly of the same scale. Therefore, food manufacturers are turning to several solutions to help solve this challenge, but there is no easy result. It is a combination of design, employment and operating decisions that hopefully add up to meeting staffing needs. Some successful manufacturing companies are combatting the skilled labour shortage by investing in automation and software to complement their existing workforce, meet production requirements, and attract new talent.
FlexPicker® Delta robot. Source: ABB
Approach to solving labour shortage
In the past, the closest thing to automatization in the food industry were processing machines and conveyor belts. Much of the process, however, relied on people. Let us take a chocolate factory as an example, where people would place ingredients then run the chocolate through a machine. From there, someone else would check the quality, and another might add the wrapper before the candy was sent to be packaged or placed on the shelves. A setting like this also adds room for mistake. If the ingredients are wrong, if the chocolate is not checked, or if a wrapper is missed; the consequences are disastrous. Thus, food manufacturers will need to source more skilled and digitally-savvy staff, including engineers and scientists, who may be hard to find due to labour shortages.
As a result, food manufacturers all over the world need access to the best talent in order to engage with new consumer trends, transform their business model, and stay ahead of the competition. But with labour shortages reported across every technical industry, where do they find that talent to grow and evolve their business? The demand for workers from processing and packaging machine operators, to plant supervisors and managers, to data scientists, have been building for over a decade; and it will not end, the population continues to grow, and people will always need to eat.
A good deal of time, energy, and money has been dedicated to figuring out what companies can do to attract and retain the workforce they need to meet the demands of the market. And the answer is that there is no easy way. There is no magical method that will make the problem go away. But there are several ways companies can both close their existing talent gaps and put themselves into a better position for the future. With the demand so high for food, automatization has become a necessity. This is where the future of automation in the food industry starts to form.
Rapid push toward automatization
The rapid push toward automatization and increased expectations of consumers and regulatory agencies for better product quality and safety has resulted in the increased adoption of automation across industries. In fact, the food automation market is expected to reach US$17.46 billion in 2026 at a compound annual growth rate (CAGR) of 9.63%, according Research and Markets.
Technological advancement is a key trend gaining popularity in the food automation market. The food market is witnessing the implementation of next-generation food automation technologies, such as robotics, digital twins, internet of things (IoT), analytics, data processing, automated control systems, and others.
Effective and efficient solution
Companies across the industry are using innovative and creative approaches to help mitigate the problem of finding staff, but most of those initiatives are short-term. Examples include increasing employee salaries or offering referral bonuses. These types of initiatives can and do work until the employee takes a better offer from another employer who is also competing over the same pool of resources. The problem is further exacerbated as that pool of resources gets smaller and smaller as experienced workers retire and others leave the industry. This is making it even more challenging to get a result from short-term initiatives.
Machine builders are already producing advanced technologies that will innovate the food industry more than ever. As food processing and packaging evolves, there will be less and less employees standing along the conveyor belt and more operators controlling the machines.
Automatization is a long-term solution to the current labour shortage problem. The equipment and lines that you invest in today will not move to a competitor if they get a better offer, and they will not transition out of the industry to work somewhere else. Instead, automatization will continue to deliver on the operational requirements of your business. Furthermore, automatization is scalable, so they can be expanded or adjusted as the needs of your business change.
The International Federation of Robotics (IFR) said the steady growth of industrial robots reflects the adoption of automation in food and beverage manufacturing, with the total global operational stock of robots increasing by 8.6% in 2020. These advanced solutions offer complete automation reducing human needs entirely and increasing profitability while ensuring safety.
For example, Pazzi Robotics, a France-based kitchen software, and robotics startup firm introduced a fully automated packaged solution for the food and beverages industry with no human intervention during the operations. The solution includes robots that perform tasks from food preparation to final assembly based on fully automated procedures. This solution uses a combination of software, data, and precision robotics.
The operational robot stock in food and beverage manufacturing steadily increased from 81,500 in 2019 to 90,100 in 2020, ReportLinker reported. This adoption was driven due to the availability of better technology, the need to stay competitive and improve workers' safety. Therefore, the rising adaptability of automation will drive the growth of the food automatization market.
In January 2022, AMF Bakery Systems Inc., a US-based automated bakery equipment solutions company acquired Workhorse Automation Inc., for an undisclosed amount. With this acquisition, AMF Bakery Systems will strengthen its product portfolio with the addition of robotics technologies and the engineering expertise of Workhorse Automation.
The iTRAK 5730 small-frame intelligent track system improves throughput in multi-product applications. Source: Rockwell Automation
Major players
Technological innovation will drive broad scale adoption of automatization in food industry, resulting in a more resilient food supply chain that produces safer products at higher volumes with reduced waste and lower operational costs, not to forget unlocking the use of automatization in most labour dependent processes. Below are some of the major players in the food automation market and their products:
ABB Ltd is expanding its FlexPicker® Delta robot portfolio with the IRB 365. With five axis and 1.5kg payload, the IRB 365 is both flexible and the fastest in its class for reorienting packaged lightweight products such as cookies, chocolates, peppers, candies, small bottles, and parcels. From product reorienting, top-loading and secondary packaging, to bottle handling, unscrambling, 3D picking, feeding and parcel sorting, the IRB 365 meets a wide variety of applications. Powered by the OmniCoreTM C30 controller - the smallest Delta robot controller on the market - the system offers best-in-class motion control, built-in digital connectivity, and 1000+ additional software hardware functions ready to meet future demands and requirements.
The global importance on reducing food loss and increasing efficiency in the food supply chain are driving food manufacturers to seek out ways to improve their production methods. The award-winning solution called Batch2Flow, designed by technology specialists from GEA Group, offers such improvements to food manufacturers. Producing formed products on high-capacity lines requires full control of the process to meet the food quality specifications each time. Big volumes mean that a lot is at stake. Therefore, quality control is key for the bottom line as well – variations in the mix at the beginning of the process will require adjustments further down the line. Too much variation in the mix can negatively influence yield, and can lead to undesired lower product quality (b-grades), less line productivity or even waste. With the automation solution Batch2Flow, the precise specifications in the recipe are continuously safeguarded, so that the desired parameters of the rest of the line can be optimally met.
Hybrid cobots to include an industry-specific version for the food industry. Source: Yaskawa Electric
Food processing applications with abrasive or viscous ingredients and strict sanitation protocols are known to be tough on conveyor belts, sometimes requiring weekly belt replacement in the most extreme conditions. Rexnord Corp., a leading multi-platform industrial company offering the broadest portfolio of conveying solutions in the food processing industry, has announced a new metal conveyor belt, the KleanTop® PacTitan Pro™. The new belt – which has been designed to not only be hygienic and food-safe, but to also last longer than belts in tough applications – offers poultry, baking and snack food processors a reliable conveying solution on applications that have typically been the most trying for belt longevity.
Food and beverage manufacturers are constantly under pressure to package a wider variety of products in more types of packaging without compromising productivity. Now they can answer these trends while increasing throughput using the new iTRAK 5730 small-frame intelligent track system from Rockwell Automation. The system uses independent cart technology to support smart, flexible and efficient machines. Independent cart technology offers many benefits over traditional gear, chain and belt conveyors, including unlimited machine flexibility, better traceability and increased uptime. By using magnetic propulsion, the individually controlled carts can quickly start and stop with high precision, which reduces machine wear and is highly energy efficient. The technology also quickly manages changeovers using pre-configured move profiles that can be implemented with the push of a button from an HMI. The iTRAK 5730 system has the smallest footprint within the Rockwell Automation independent cart portfolio. It has a 50 mm minimum pitch that makes it ideal for primary packaging applications, such as flow wrapping, end load cartoning, and form-fill-and-seal pouching. The system also easily integrates into a manufacturer’s architecture, providing analytics that help optimize energy use, monitor parts wear, and reduce downtime.
Boost manufacturing flexibility and efficiency. Source: Schneider Electric
Schneider Electric creates next-generation Food and Beverage industries with EcoStruxure. Building the next-generation food and beverage systems requires bold moves. The company has the opportunity to accelerate the drive toward a zero-emission future, to improve agility and profitability, and to meet end consumers' expectations for safety, sustainability, and transparency. Together with its partners, Schneider Electric delivers digital energy management and automation solutions to achieve the next generation of efficiency, resilience, and sustainability for the industry that feeds the world.
The MOTOMAN HC10DTF extends the Yaskawa Electric portfolio of hybrid cobots to include an industry-specific version for the food industry. Like the currently available HRC-capable designs HC10DT IP67 and HC20DT IP67 the new product is also in dust- and watertight according to protection class IP67. However, in addition the new robot has a powder-coated surface that permits the use of alkaline and acidic cleaning agents. In addition, it uses food-safe lubricating grease. The MOTOMAN HC10DTF thus fulfils the stringent hygienic requirements of the food and pharmaceutical industry pursuant to ISO Class 5 or EG-GMP Class A. It can therefore be used, for example, for palletizing primary packaged food or handling samples in laboratories. Employees can be relieved of physically stressful work, e.g. stacking larger cardboard boxes or other stackable goods. The robot assumes the task of lifting these heavy loads, improving workplace ergonomics, and personnel can be deployed to cognitively more challenging activities. Like all models in the MOTOMAN HC series, the new HC10DTF is also an HRC-capable hybrid robot. This means that it can be also be operated in hybrid mode by connecting external safety technology, e.g. a laser scanner. As a result, the cobot alternates between collaborating, reduced and full speed, in order to achieve a maximum cycle time depending on the distance to the operator.
FANUC SCARA robots ideal for food and cleanroom applications
FANUC is now pitching its technology advantages to the food industry with the release of two new models. Offering a highly competitive price-to-performance ratio, the FANUC SR-3iA/C and SR-6iA/C provide users with a number of special features that make these fast and precise SCARA robots ideal for use in food plants and cleanrooms. The new SR-3iA/C (3kg payload, 400mm reach) and SR-6iA/C (6kg payload, 650mm reach) use the same mechanical structure as FANUC’s proven and highly successful SCARA range. However, there are also several notable differences, such as a white epoxy coating for extra durability in severe environments, and an IP54 protection rating that guards against the ingress of contamination from dust and water spray. The latter makes the robots suitable for use in food plants and cleanrooms that require clean-down procedures. As a point of note, a special bellow protects the operation-critical spindle during cleaning, setting it apart from competitor SCARA robots. Further features that promote the SR-3iA/C and SR-6iA/C as ideal candidates for food processing facilities and cleanrooms include the standard use of food-grade grease certified to NSF-H1, along with anti-rust bolts, both of which are essential in food handling applications.
SoftAI Solutions accelerates adoption of robotics in food processing. Source: Soft Robotics
The SoftAI Solutions from Soft Robotics incorporates proprietary 3D vision, artificial intelligence software, and industry-proven soft grasping to address the most pressing problem plaguing the food industry – the inability to meaningfully automate operations. SoftAI augments traditional industrial robots with true hand-eye coordination unlocking their use in most labour-dependent processes. This technological innovation will finally drive broad scale adoption of automation resulting in a more resilient food supply chain that produces safer products at higher volumes with reduced waste and lower operational costs. "The food industry is critically dependent on labor to meet its production goals," says Mark Chiappetta, COO at Soft Robotics. "But, challenges with workforce availability and productivity, tightening food safety regulations and global health crises have illuminated the need to break this dependency. SoftAI powered robotic automation is the solution."
Conclusion
When you cannot find the talent you need due to the labour shortage, the answer is increasingly clear: automatization. In fact, some of the companies better positioned to weather the labour shortage have already automated workflows to become more efficient. But automatization does not only help fill the labor shortage, it also leads to job openings. In many situations, the aim of automatization is not to replace workers. This is a common misconception, particularly with those outside the industry. The more pressing priority for food manufacturers is optimizing how they use existing resources. After all, food will always involve people from harvesting, processing, and cooking. Automatization will not remove the human factor from the food industry. Rather, it is calling for a new set of skills, such as greater efficiency in machinery. Skill level is an important consideration, too, as there are now automation technologies that make it possible for food manufacturers to hire staff with lower levels of skills. This is another way that automation is helping food processors minimise the impact of labour shortages. Yes, automatization may replace some jobs. But in the end, automatization paves the way for innovation, creating opportunities for more people to find better work, and allows businesses to remain competitive and productive.