www.ptreview.co.uk
30
'23
Written on Modified on
OMRON Transforms Logistics for a Dynamic Industry 4.0 Landscape
Boosting Efficiency and Employee Satisfaction in Manufacturing and Warehouse Management.
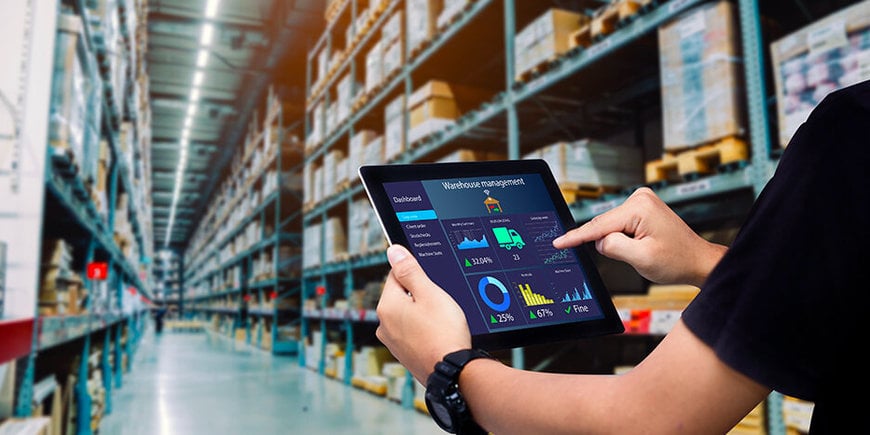
In addition, relying solely on human experience not only increases the psychological burden on workers, but also increases the risk of human errors fatal to the manufacturing and distribution sectors. Co-creation of safety by human and machine that OMRON aims to promote is helping to solve these challenges faced by the production and logistics. In this article, we feature the story of innovative impact, which made a difference in Garnet's production process.
Garnet's logistics process was a big headache
Garnet is a Europe-based importer and distributor mainly in the areas of automation and robotics, providing a wide variety of components to various manufacturers internationally. Their lineup includes sets of motors and drivers, combinations of encoders and resolvers, power semiconductors, plastic ball screws, linear actuators, among many other things, and the logistics process was a big headache for them.
There was an immediate need to bring efficiency in work practices and less reliance on the experience of skilled workers. A large variety of parts were picked by the workers who looked at them. They then pushed a heavy cart in a vast warehouse and walked quite a while to an assigned place. They were confined to the environment where simple but demanding tasks were repeated.
The process which depends largely on the experience of the workers and repeats physically demanding tasks not only increases the risk of human errors but also reduces employee motivation. Moreover, it hinders productivity to a great extent. Therefore, Garnet began to look for a partner who could jointly harness Industry 4.0 and address these challenges through integrated and rapid automated solutions.
OMRON and FasThink Combining best of both worlds
These challenges were addressed by OMRON and digital native company FasThink. Together, they aimed to realize an integrated manufacturing and logistics solution. The team focused on monitoring the progress of the logistics process in real time and automatically detect various components so as to automate physical picking process. Their aim was also to smoothly replenish and distribute parts inside the warehouse in order to free the workers from the burden.
To this end, OMRON and FasThink combined their strengths to innovate. FasThink's primary focus is the integration of field technologies for process improvement in the logistics and manufacturing. Their innovative P2Light (Pick-to-Light) technology is an application optimizing the processes of parts picking and handling, revolutionizing digital processing for many companies. OMRON, on the other hand, is the one and only provider in the world to offer a complete portfolio of solutions such as sensors, robotics, and automation platforms. When these two companies work in collaboration, all logistics processes can be integrally controlled, and a wide range of tasks can be fully automated.
P2Light is an intuitive order picking system that avoids handling errors by the operator. As soon as an order number is scanned, the system turns on lights guiding the operator to the picking location, while simultaneously confirming the picking via a non-contact sensor.
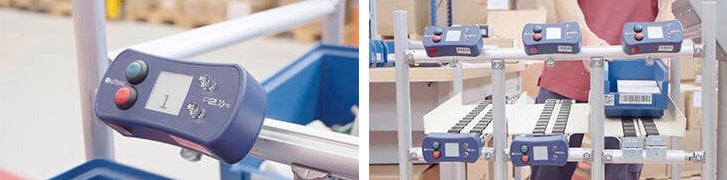
Navigating to Productivity with Mobile Robots
OMRON's AMR (Autonomous Mobile Robot) is a robot that can autonomously navigate throughout plant and warehouse. Thanks to safety systems and sophisticated algorithms, it can work collaboratively with an operator. By integrating FasThink's P2Light technology and Warehouse Management System (WMS) to the robotic system, picking work performed by the robot can be checked on the application, and this allows easy operation and control for the workers.
"The robot is equipped with a series of innovative P2Light devices that guide the workers via visual signals to a pickup location as part of the picking process. Once the picking order is fulfilled, the mobile robot all by itself carries all the parts to the next step of logistics following the order process. This new process not only minimizes the risk of errors during order preparation and reduces picking times, but also eliminates the need for order pickers to carry heavy loads and walk long distances on the site. In this way, Garnet was able to free the workers, enabling them to focus on value-added activities rather than handling manual work," The positive impact created by the system on the workers was emphasized by Luca Fraticelli, Systems Integrator Manager at OMRON Electronics Italia, as follows.
Sustainable transformation
The work of OMRON and FasThink brought about the automated solution for Garnet, resulting in a dramatic transformation of their logistics process. Garnet's new logistics process significantly reduced the distance the workers had to walk each day, which was about 10 kilometers, for moving parts. Moreover, now there are fewer picking errors, shorter picking times as well as an accumulation of various data allowing the logistics process more flexible and traceability more robust.
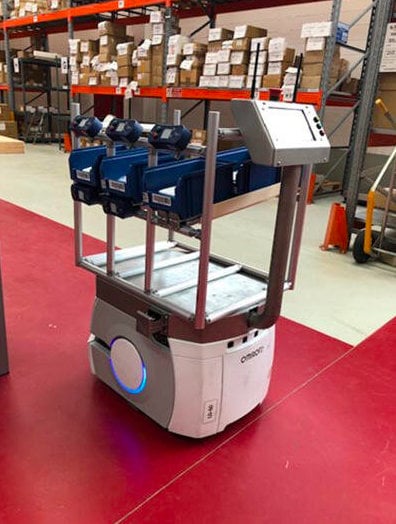
Pick2Light system and Omron Mobile Robot for Garnet
"The innovative aspect brought about by Industry 4.0 allowed us to overcome issues related to the logistics and production in entirely new ways. We now feel ready to address the challenges the market will pose to us in the near future, such as how quickly and flexibly we should be able to adapt to changes and boost employer attractiveness," Leopold Lurino, Chief Executive Officer (CEO) of Garnet evaluates this effort as follows.
"The starting point of OMRON's innovation is based on the principle that we want to improve lives of people and make society better via automation. In Garnet's case, the safe and user-friendly solution was developed to alleviate the burden on the workers, making the work more enjoyable while increasing efficiency. These days, it is becoming harder to secure experienced talent. So, industrial automation is such an important tool since it creates an environment that is easy for inexperienced plant laborers and operators to engage in their tasks. Further, it cuts down wrongly-processed orders as a result of reduced picking errors, and also by eliminating unnecessary transportation, it reduces the carbon footprint arising from the consequential operations of Garnet and its client," Innovation 4.0 is not just about boosting productivity. Marco Mina, Key Account Manager, Robotic Solutions at Omron Electronics Italia said as follows.
Exploiting its strength in automation technology, OMRON continues to contribute, through its business, to the evolution of a sustainable industry by pursuing both happiness of all working people and advancement in industries.
www.omron.com