www.ptreview.co.uk
24
'20
Written on Modified on
FTI squeezes time-to-market for sheet metal parts with 3D die scanning and design productivity tools
Forming Technologies (FTI), part of Hexagon’s Manufacturing Intelligence division, has announced new virtual manufacturing capabilities that improve productivity setting up sheet metal process simulation with CAD design interoperability and Hexagon 3D scanning.
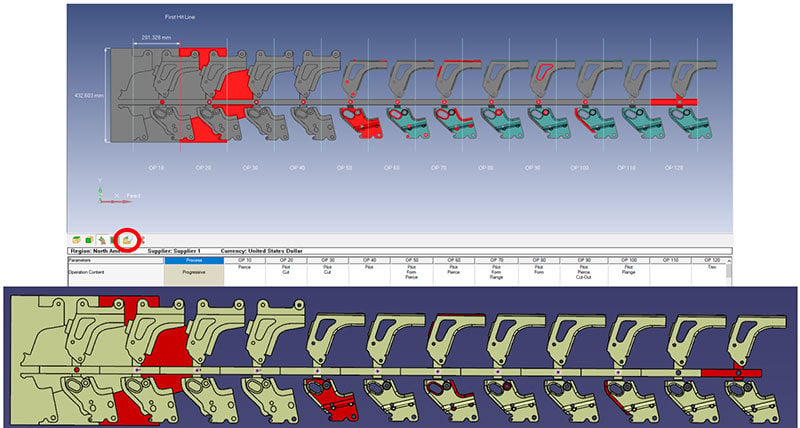
FTI’s FormingSuite software helps manufacturers to evaluate the cost of tooling and material in sheet metal processes, assess the feasibility of designs to avoid costly product changes and reduce time to market. Its FormingSuite 2020 release introduces features that enable cost engineers, designers and die-makers to work more productively together throughout early product design and improve the accuracy of virtual try-out.
Stamping dies are frequently modified through grinding and spotting during try-out, before they are put into production, which renders CAD designs obsolete. For the first time, users can now connect FormingSuite to Hexagon’s 3D metrology systems so that any die can be quickly scanned to capture these modifications and feed real manufacturing parameters back into virtual try-outs. This scanned data is then used directly in simulations to perform accurate validation of the stamping process.
Some stampers require the ability to run two different shaped blanks in their transfer presses. These lines are equipped with advanced features such as oscillating shears, indexing conveyors, and rotate stations so the stamper also can process rectangle, trapezoid, mitre, parallelogram, and developed (shaped) blanks into the same large-bed press.
A new workflow provides easy setup to optimize the cost and tooling for processes with two unique coils. Furthermore, engineers can now save time by optimizing conceptual designs for manufacture in FormingSuite, then exporting the blanking die process geometry from the transfer die layout and the progressive die strip layout directly to their CAD system to use as the basis for their design.
New features make it easier for manufacturers to set up more accurate process simulations by automating repetitive tasks and more flexible design tools. A powerful new Sketch Web tool provides engineers a fast and accurate way to create custom web designs outside of standard shapes. Furthermore, automatic and user-defined mesh refinement for trimming improves the precision of die models. When evaluating materials utilization, design changes can now be automatically applied to the opposite, symmetrical side of the part. These improvements, combined with refinements to the software’s calculation and costing methods, enable manufacturers to make better manufacturing decisions at the design stage.
Andy Melang, Business Development Manager at Ultratech, commented: “One of our customers came to us for a small bracket that is a late add to a new frame. Most of the tooling for the frame was built in China, but due to time restrictions they re-shored it locally and needed quotes immediately as the tool needed to be built in 12-16 weeks. Using FormingSuite COSTOPTIMIZER Professional, the time from them saying ‘we need this part’ to the time we sent the total cost with cost breakdown was a couple of hours. I didn’t have a day or two to get assistance from our tool designer, but because we could turn this around so quickly it not only looks like we want the job, but we look professional doing it.”
“Approximately 70% of decisions related to the overall cost have already been committed in the early design phase and optimizing forming delivers a high return for high volume manufacturing,” commented Hendrik Schafstall, CEO. “Our goal remains to be intuitive and accessible to everyone that needs better process knowledge, not necessarily CAE experts. FormingSuite’s new features improve the productivity – and the competitiveness – of our customers by speeding up their time to market with better decision making upfront.”
www.hexagonmi.com