www.ptreview.co.uk
10
'20
Written on Modified on
TooLink - connecting tools with die-cutters
BOBST’s latest digital solution – TooLink - is drastically reducing changeover times by connecting tooling, machinery and processes, helping converters who are under pressure to deliver smaller runs with a quicker turnaround time.
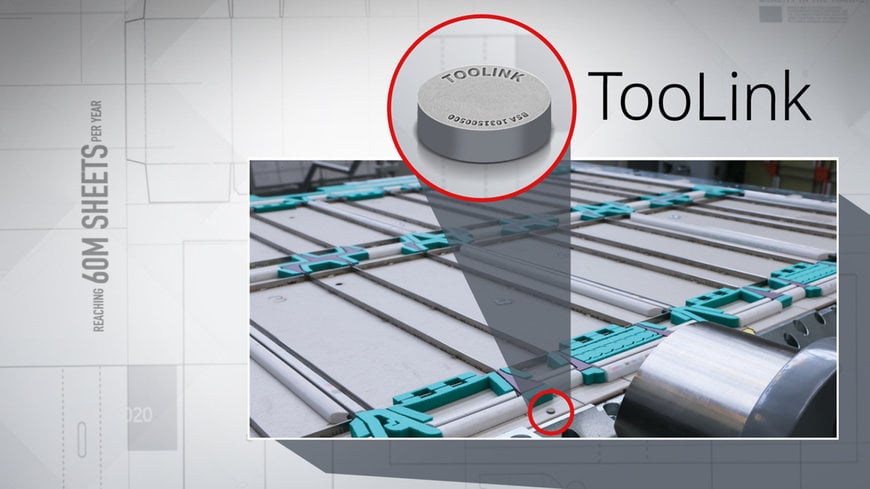
Reflecting BOBST’s vision to shape the future of the packaging world, tools connecting with die-cutters sets a new standard for efficient and agile box converting. Thanks to the utilization of digitalization and connectivity, converters have the means to become more productive.
TooLink simplifies the change-over by automating the recipe management, which saves time for the operator and removes the risk of human errors.
“In our discussions with customers, we hear that the downtime from one job to another is still taking too long, which is reducing valuable production time,” says Alex Volery, Head of the Tooling division at BOBST. “We saw the opportunity to develop a digital and automated solution to help overcome this issue, hence we have developed TooLink.”
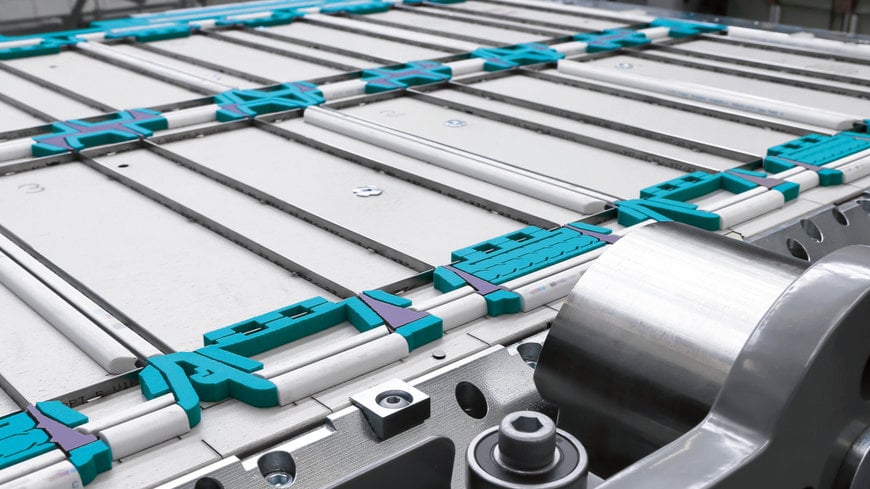
A secured data chip is built into the die and creates a unique ID for every tool. When the tool is inserted in the machine the chip is read and the production-ready recipe with correct alignment and settings is automatically transferred to the machine. All it takes for the operator is two clicks on the die-cutter’s HMI, allowing a significant saving of changeover time on repetitive jobs, as well as potential operator mistake when inserting the recipe.
TooLink-prepared tools are manufactured by a BOBST Certified Die-maker, ensuring that both the quality of the tool and the compatibility with the die-cutter is maximized.
“This is the first phase in our development of the TooLink technology”, continues Alex Volery. “We are hard at work developing future added-value services and solutions related to tooling connectivity. The various stakeholders will be connected, tooling and recipe management will be done remotely and access to tooling data will leverage insights. These digital solutions will empower better decision-making and deliver increased control, automation, and efficiency.”
All new BOBST 106 format die-cutters are TooLink ready and in combination with Matic Plus the saving of repetitive job changeover time is estimated to an average of 15 minutes. It provides converters with valuable additional production time and flexibility.
www.bobst.com