www.ptreview.co.uk
14
'20
Written on Modified on
More and more plastics manufacturers rely on GEA separators in the production of polycarbonates
Everyone encounters them every day: products made of polycarbonate can be found as eyeglass lenses, car headlights, glass pane replacements or Lego building blocks.
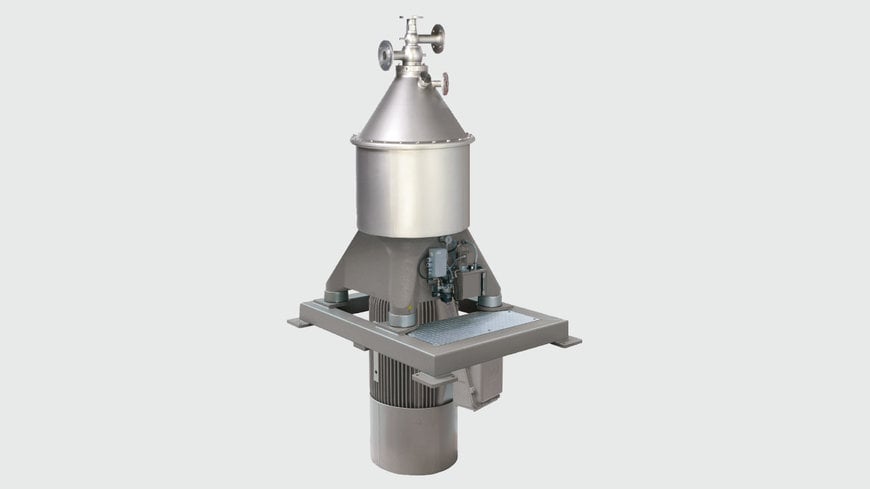
Polycarbonates are also used in large quantities for stadium roofs, conservatories, solar panels and many components in the electrical industry. They have even found their place in the production of medical products. In short, the use of polycarbonates, thanks to their strength and transparency, enables numerous technological advances, new design solutions and improved performance, and simplifies the mass production of numerous consumer products.
In the production process of polycarbonates, separators from the mechanical and plant engineering company GEA play a decisive role due to their mature technology, the qualitatively very pure separation result, their high level of safety when handling hazardous extraction media, and last but not least their associated robustness. More and more customers worldwide, and for some years now especially in China, are opting for GEA's technological solutions in the production of polycarbonates. GEA is thus further expanding its good market position in the production of polycarbonates.
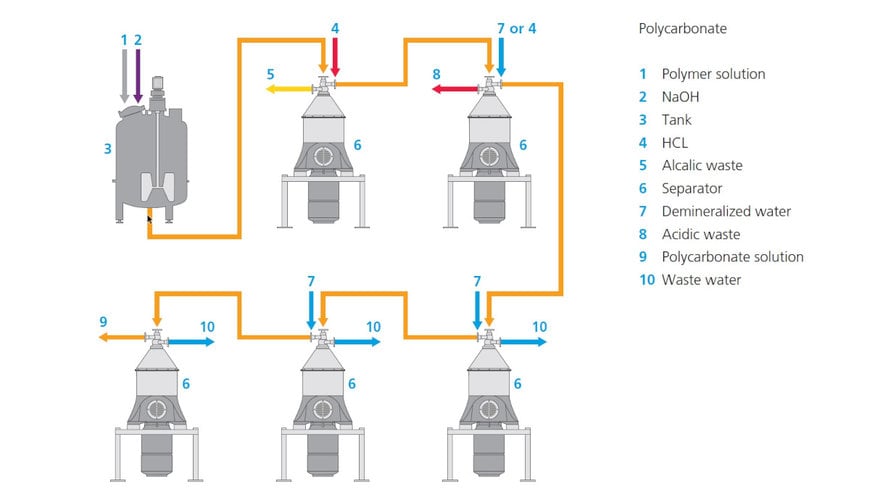
The process in the production of polycarbonate.
Separators from GEA in the phase interface process
Polycarbonates (abbreviation PC) are thermoplastics. The production of polycarbonate by the phase boundary surface method is of great technical importance. Here a reaction of phosgene with bisphenol A takes place, with the addition of NaOH and organic solvents. In a multi-stage extraction process, the polycarbonate solution produced by polycondensation is washed in a separator system in a neutral and electrolyte-free manner. Acids and demineralized water are added in the individual washing stages to wash out residual catalysts, reaction by-products and other impurities.
Especially in the separators with full-jacket bowl used in the acid stages, all components coming into contact with the product are protected by highly corrosion-resistant materials to ensure long service lives. The result of the extractive washing process is a practically electrolyte-free solution of polycarbonate in the solvent, from which the high-purity polycarbonate is obtained in the subsequent process stages. In this way, the polycarbonates obtained with the help of GEA separators meet the highest quality standards.
Highest safety and performance
Polycarbonate manufacturers worldwide appreciate the high degree of purity of GEA separators and thus the high clarification efficiency and the complete fulfillment of the complex safety requirements in the chemical industry. GEA process specialists support the customer right from the start of a project with technical competence and expertise. To ensure optimal process and plant solutions, process specialists work in dedicated project teams with the customer at every stage of the project - from planning to plant commissioning - to ensure that the project is completed on schedule and all Key Performance Indicators (KPIs) are met. A comprehensive service and upgrade program is also available to ensure plant performance and longevity.
Safety for man and machine with top priority
The aspect of safety naturally has the highest priority in such plants in the chemical industry. Where concentrated acids, pressurized, flammable and explosive substances are part of daily production, the requirements for the design of a separator are extremely demanding. GEA separators and decanters designed specifically for processes in the chemical industry successfully meet these special requirements and are selected according to the necessities in the customer process.
www.gea.com