www.ptreview.co.uk
06
'21
Written on Modified on
NSK, the driving force behind NWG
The NSK plant in Munderkingen, Germany, specialises in manufacturing the company’s full range of double row ball bearings, around 30% of which carry the NWG (Neuweg) branding. Double row ball bearings find their way into all kinds of industrial applications, everything from motorcycles and vacuum pumps, through to surgical power tools and film-making equipment.
Manufacturers across Europe seeking value-added bearing solutions have long relied upon the Neuweg brand for performance and quality as it has been part of the NSK group since 1990. As a result, users of NWG-marked bearings not only benefit from products manufactured according to NSK standards, but can tap into the innovation and customisation capabilities of a global bearing specialist with more than a century of knowledge and expertise.Double row ball bearings produced at the facility include self-aligning, angular contact and deep groove types. However, beyond the standard range, a specialty of the plant is its ability to manufacture variant designs in short lead times.
Customisation options
In terms of the outer ring, customers are able to request a specific diameter and width, as well as requirements for a groove or threaded bore. It is also possible to select special profiles, such as spherical, Gothic arch, V and groove, while specific diameters, cones, teeth, grooves and threads are among the customisation options for the inner ring bore. In addition, various special seal options are available, like multi-lipped, labyrinth and three-part, along with several coating choices. A new option here is DLC (Diamond-like Carbon) coating, an ultra-thin layer (1-3 µm) that provides superior wear resistance thanks to its high hardness (70 HRc).
Among the major competence areas at the Germany-based NSK plant is the agriculture industry, which has special requirements for protection against dust, dirt and shock loads. NSK has developed solutions that can cope with these harsh conditions, which include not just bearings, but fully built units like Agri Disc Hubs. These ready-to-install bearing units offer high efficiency and a robust sealing system, ensuring their success in machinery such as compact disc harrows.
Retaining the agriculture theme, NSK has developed many special bearings over the years for this demanding sector. A case in point was a special NWG series double row ball bearing (with integrated flange) required by a major agricultural machinery OEM for a high-capacity pneumatic seed drill. Alongside design innovation, high performance and reliability were among the principal factors governing selection.
Pumps and compressors provide another focus market. For these products, the Neuweg plant develops and manufactures double row angular contact ball bearings both in standard and special format, as well as QJ bearings (four-point contact bearings) in a broad range of variants.
To offer a further example, a leading woodworking machine OEM is taking advantage of a special double row angular contact ball bearing for a range of sliding table saws. The bearing features a V groove on the outer ring, along with customised dimensions and axial clearance.
Additional products manufactured at Munderkingen include support rollers and pulleys, which serve high-temperature furnaces in the steel industry, for example.
Supply chain security
A key benefit for European customers of the solutions produced in Munderkingen is rapid delivery. Located in the south of Germany, the plant has excellent access to Europe’s wider transportation network, reducing any risk of supply chain disruption.
The manufacturing expertise of NSK has had a huge influence on the Neuweg brand. Thanks to the introduction of modern manufacturing strategies and processes, the Munderkingen plant can offer high levels of flexibility. It is possible to produce a vast range of products, even in small-to-medium batch sizes (from 1000-off), providing yet another benefit for customers seeking bespoke solutions. Using NSK’s expertise in engineering and innovation, special designs can progress from concept to production in just 2-5 months.
NSK can cite many, many examples of customised bearing solutions that have been developed and manufactured at Munderkingen. For instance, these products include: a fully integrated flange bearing for an elevator gearbox and a double four-point contact ball bearing with split inner ring for a mobile crane. Further examples of bespoke double row angular contact ball bearings include ones with a 35° contact angle and split inner ring for air conditioner compressors used on commercial vehicles, others offering a 25° contact angle and extended inner ring for surgical power tools, ones featuring a fully integrated flange and special sealing for a vacuum pump, and yet more with a low-friction TM seal and high-temperature plastic cage for a motorcycle gearbox. The plant has even produced support rollers for so-called ‘sky cams’ that suspend over the playing surface at major sporting events.
It is important for the market to understand that it is possible to propose and manufacture high added-value bearings within the NSK group, helping customers to save money through the provision of solutions that take full lifetime costs into account.
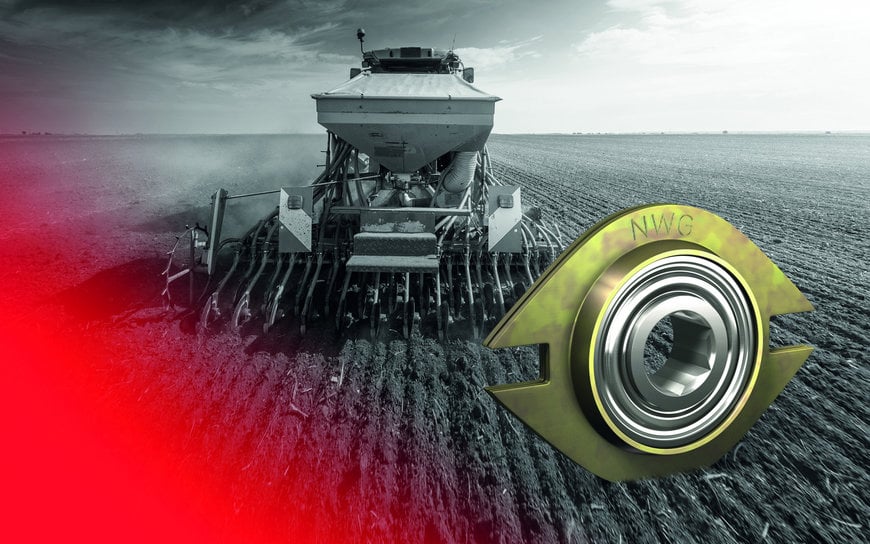
2) This customised double row angular contact ball bearing is proving ideal for a sliding table saw used in woodworking
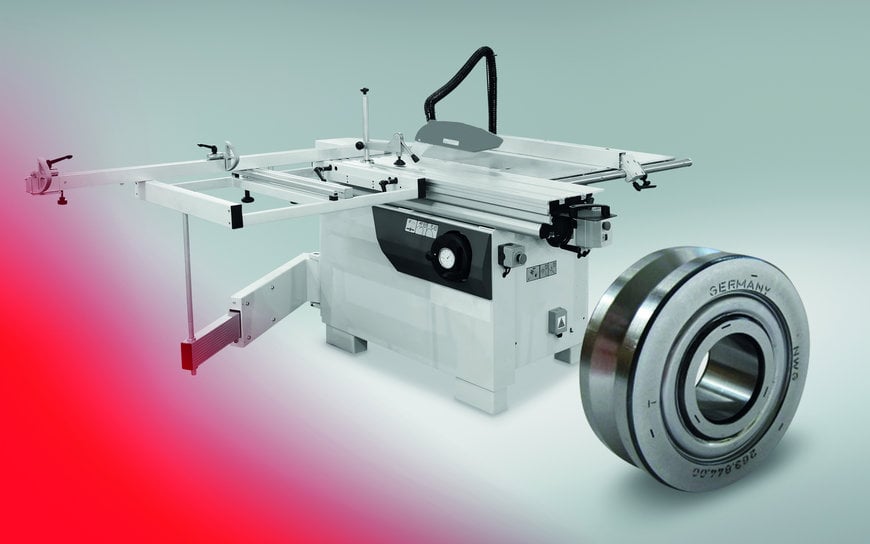
3) Around 30% of the products produced at NSK’s Munderkingen plant feature the NWG marking
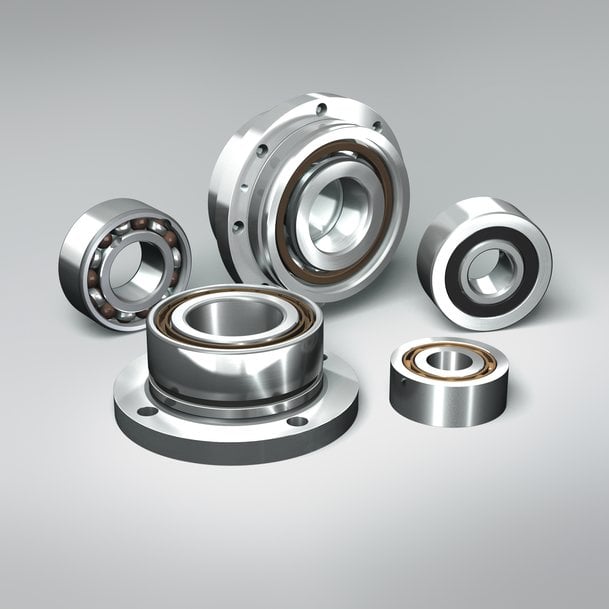
4) Pumps and compressors provide a focus area for double row angular contact ball bearings
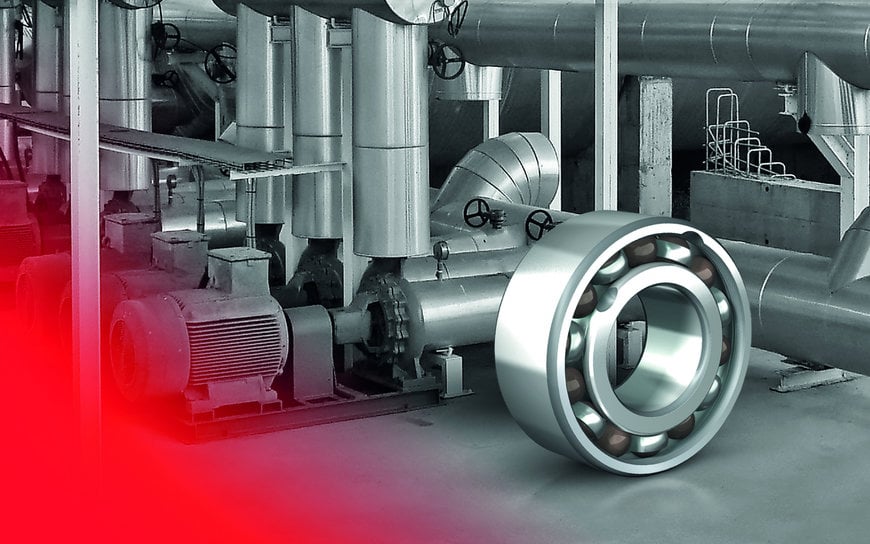