R+W LINE SHAFTS – FOR LONG DISTANCE MECHANICAL SYNCHRONIZATION MODEL EZ/ZA
Whether for a multi-jack lift system, servo driven gantry robot, or any number of other types of specialty machine designs, engineers are frequently faced with the need to create synchronized motion in multiple locations.
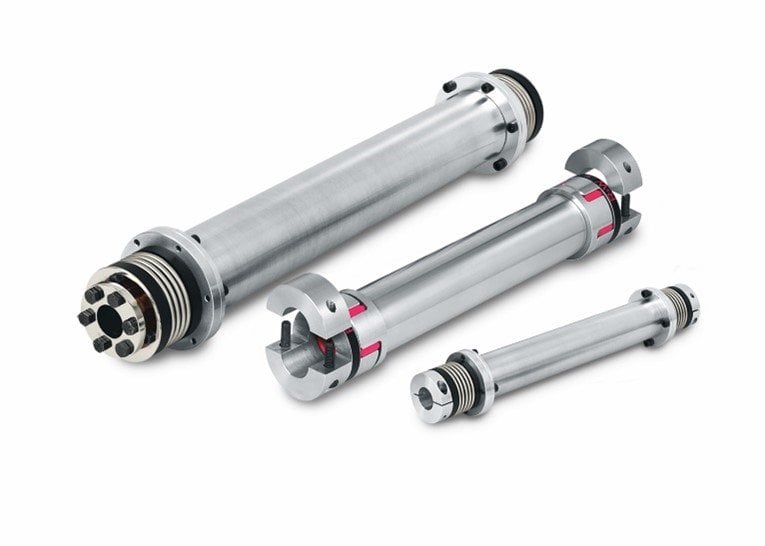
The first approaches are often to consider multiple motors running the same motion profile, or to make something out of shafting, bearings, and couplings. But there is a ready-made design that can save time and money while also providing for a more elegant solution.
R+W model EZ and ZA line shafts are constructed of light weight, laterally stiff, and highly straight drive shaft tubing, fabricated to length, with zero backlash flexible couplings mounted to each end. Overall lengths of 6 meters and more are possible, depending on the torque and speed requirements. After a quick consultation, R+W can recommend the most efficient size and material for the intermediate tubing to help ensure smooth, stable running. The three main flexible coupling types available for the ends include precision elastomer jaw couplings, torsionally stiff bellows couplings, and high-capacity disc pack couplings.
Elastomer jaw coupling line shafts are most often the best choice for multi-jack lift systems. They represent the lowest cost of the three types, and in many lift system designs the high torsional stiffness of bellows or disc pack style couplings is not needed, since torsional wind-up in the couplings is mitigated by the mechanical ratio of the jack. In lift system applications the cost of the line shaft coupling is often less than that of purchasing couplings, shafting, bearings, bolts, keys, etc., not to mention the labor time savings that result from the simple drop-in mounting facilitated by the line shaft.
When a little more torsional stiffness is needed, for example when linking two servo driven belt drive actuators to form the base X+X’ level of a gantry system, bellows style line shafts can be a good choice. The high torsional stiffness can help keep the wind-up to down to a fraction of a degree, even under peak loads, which helps to support dynamic movement while keeping the actuators well synchronized. While a little more costly, the mechanical synchronization can be made nearly perfect when center driven by a common motor and gearbox with a dual shaft output, and with two bellows style line shafts bridging the distance to the actuators. Here too the cost of the hardware is still normally well below the alternative of powering the two actuators with two separate motors.
Disc pack couplings are often used for the most demanding line shaft applications. The significant technical difference is that the flexible joints are each laterally stiff, and only offer a pivot angle at each end. This means that even though the line shaft assembly is capable of compensating for misalignment between the shaft ends, they still hold the intermediate tubing rigidly inline during rotation.
This style of coupling is used for a variety of industrial applications with large length, torque, and speed requirements. These can include larger material handling systems, cooling tower drives, and high-performance mechanical test benches, to name a few areas of application. The disc pack style line shaft is also the most common type of the three to be custom made with carbon fiber drive shaft tubing to allow for longer length shafts to run stably at a given speed – though all three types are available with this option.
R+W EZ/ZA Line Shaft Couplings at a Glance:
- Up to 6 meters long without intermediate support needed
- Cut to length with easy drop-in installation
- Multiple coupling styles and tube materials available
- Inch and metric bore diameters from 5mm to 5.5”
- Torque capacities ranging from 9 to 25,000 Nm