www.ptreview.co.uk
05
'21
Written on Modified on
Fit for forming and inspecting pressfittings
A Spanish manufacturer of high-quality stainless steel pressfittings has automated the forming and the in-line quality control of bent tubes made from stainless steel. Laser vision-based bin-picking, automated inspection and clever co-operation of two different types of Stäubli robots (six-axis and scara) are among the technologies used.
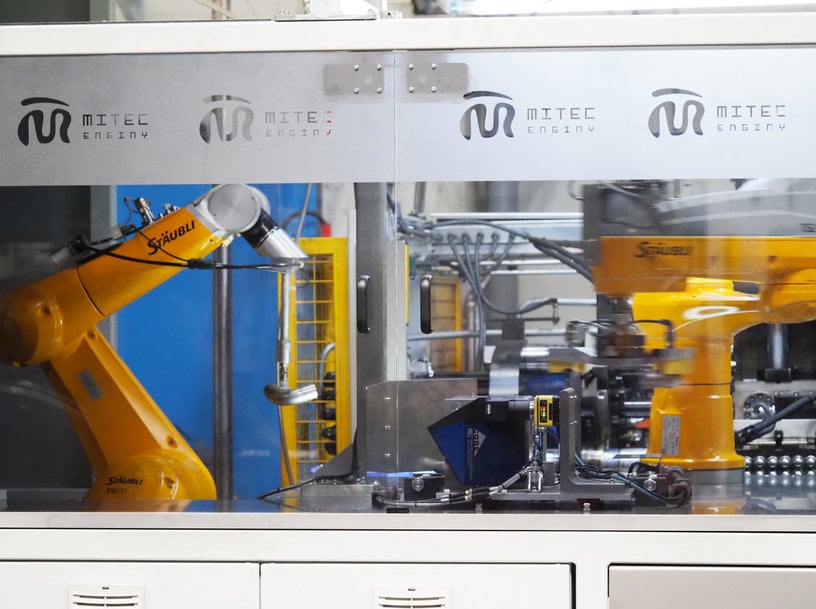
No welding, easy installation, safe and leakage-free operation during many years: these are the three advantages of stainless steel pressfittings. These fittings find a broad range of use in, for instance, buildings (water and gas installation, heating), industry (compressed air, process gases) and heavy-duty applications like shipbuilding, mining and offshore technology.
Three million pressfittings per year – used all over the world
The Spanish company Isotubi, based in Castellbisbal near Barcelona, has a high reputation in manufacturing these safety-related fittings. Founded in 1976 and family-owned in second generation, Isotubi processes 5,000 tons of stainless steel tubes per year and manufactures three million pressfittings. More than two thirds of them are exported, and the list of export countries ranges from Angola and Australia to Ukraine and USA.
Three million pieces in one year: this means that each day more than 11,000 fittings are produced by a total of 120 employees. So, automation is a must and it starts with automated cutting and bending machines. In the next step, the typical profiles are formed. They will ensure that the fittings are tight and safe for years after the pressing tool has connected them on-site. Finally the pieces are cleaned and degreased. Once all this is done, the pieces are heat treated in a vacuum oven to bring their mechanical properties back to their initial values.
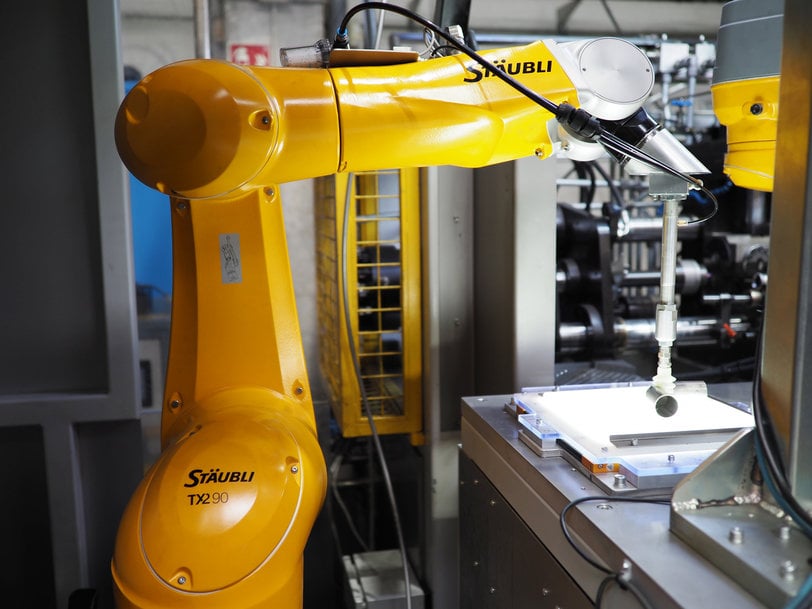
Scanner-based bin-picking with bent tubes
As a pressfitting is necessary each time when there is a bend in the piping, bent pieces or “elbows” from stainless steel are among the major products in the Castellbisbal factory. And although the geometry of the bends – together with the round diameter of the fittings – do not encourage or facilitate automation, Isotubi has achieved to automate their forming and inspection process: with the help of Stäubli robots.
The process is as follows: a Stäubli six-axis TX2-90L robot picks the bent pieces from a container. Here, a dedicated bin-picking system – developed by Isotubi in partnership with BCN VISION and using a Photoneo laser scanner – serves as the „eye“ of automation. The scanner scans the content of the container and creates an image. The vision software calculates the position of reachable pieces and sends the appropriate position data to the TX2-90L robot.
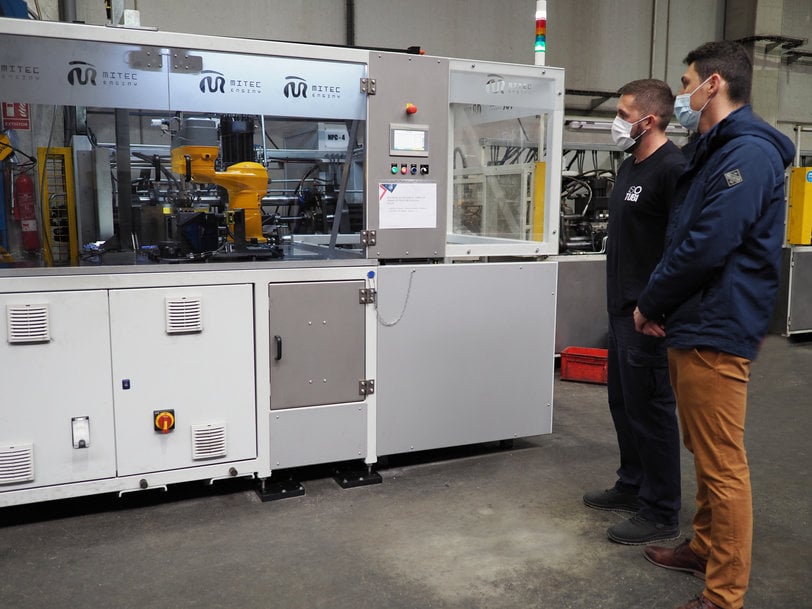
Loading and unloading the forming machine
The robot chooses the piece that is easiest to handle, grips it and brings it to a middle station where the bent piece is layed on the optimal position for further processing. Then the second robot, a TS2-80 scara, loads the piece into the forming machine. After the forming process, the same robot unloads the finished piece, and the process starts again within a very short cycle time.
While the next forming process is in progress, the TS2-80 takes the piece that was bent just before to an in-line inspection station. Here, a camera controls its dimension after production and makes sure that the piece is o.k. After this, the fast and precise TS2-80 unloads the quality control station and places the bent piece onto a conveying system which leads to the heat treatment. This station has also been developed in co-operation with BCN VISION.
The complete automation cell – which is, by the way, very compact in its dimensions – has been designed and built by MITEC ENGINY, an engineering company based in Girona/ Spain.
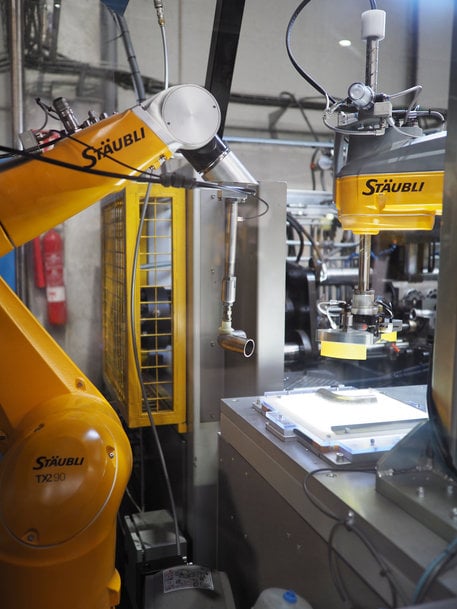
“Division of labour” with two types of robots
All in all, the two different robots and their cleverly designed “division of labor” make sure that a high degree of automation and, at the same time, high productivity is achieved. Héctor Bentué , Chief Operating Officer and Alberto Fernández, Process Manager at Isotubi: “The combination is ideal, MITEC did a very good job: on the one hand, the TX2-90L has an impressive dexterity that allows the robot to empty the container by laser-based vision completely. On the other hand, the cycle time of the TS2-80 scara robot is fast enough to perform the handling task in a shorter time than the process cycle of the forming machine. Thanks to that, the robots are not adding time to the machine cycle – a very efficient solution.”
For Isotubi, one main reason for automation is that the robots bring stability and consistency into the process. The main goal, of course, is to increase the productivity – with an automatic loading and unloading system that is also able to integrate the in-line inspection system. In this way, the two robots are handling 100% of the production in two stations, one for production and one for quality control.
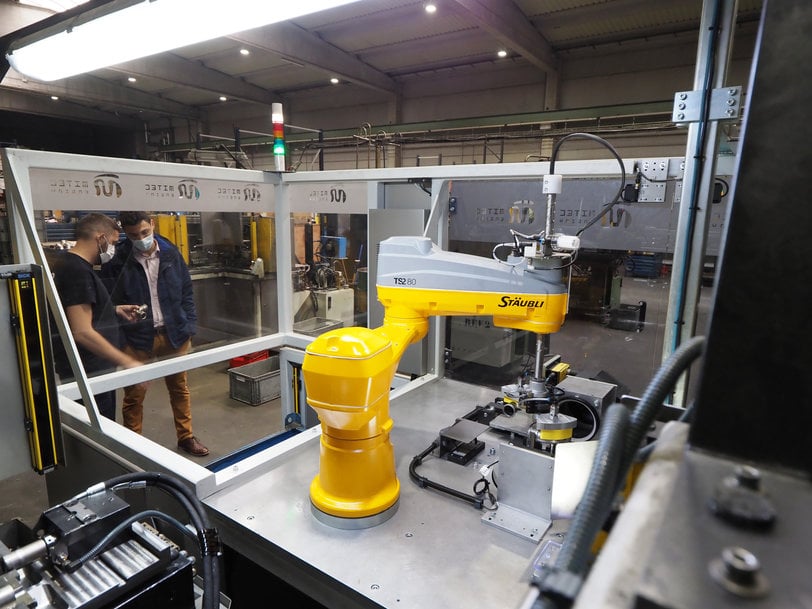
Héctor Bentué: “At same time, it was crucial for us to use an automation solution that is easily adaptable to new models with different diameters and lengths.” This requirement is fulfilled, too: via Stäubli’s CS9 control system, the robots can be programmed easily and on the same user interface.
One question remains: why did Isotubi opt for Stäubli robots? Héctor Bentué : “The specialists from our partner MITEC ENGINY recommended them for their good performance, stability and versatility – and they were right.”
www.staubli.com