www.ptreview.co.uk
07
'21
Written on Modified on
EMO premiere of the TNC7 from HEIDENHAIN: the new level of CNC control
At EMO 2021, HEIDENHAIN will be entering a new chapter in shopfloor-centered manufacturing with the new TNC7. This standard-setting CNC control supports users from initial design to final machining, from one-off jobs to serial production, and from simple slots to complex contours.
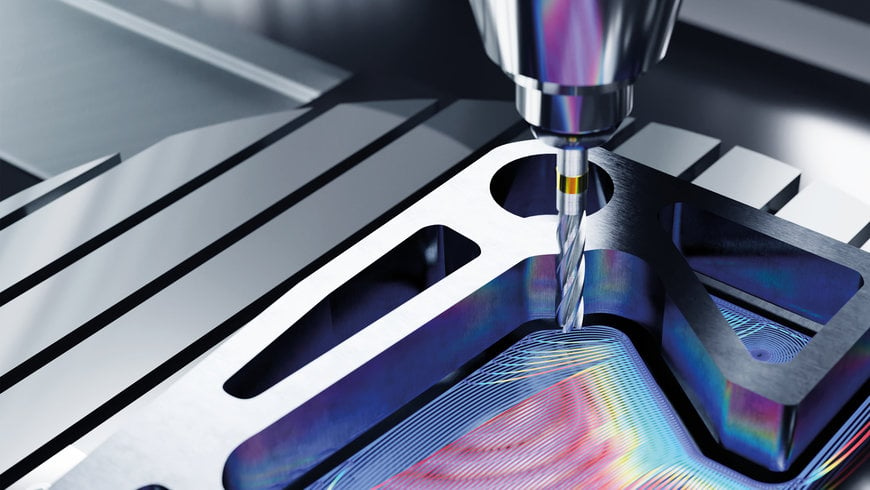
Its groundbreaking control platform lets machine manufacturers adapt the user interface to their machines and offers dynamic development potential for even greater functionality.
The HEIDENHAIN TNC7: the future of CNC control
The TNC7 from HEIDENHAIN delivers an outstanding user experience, bringing new possibilities to users on the shop floor. Along with easy and intuitive operation, users enjoy support from a virtual simulation of the machined part and work envelope. The TNC7 also leverages pioneering machining strategies and powerful functions for process reliability and optimization. This new level of CNC control enhances daily work with carefully crafted, task-focused solutions, combining familiar Klartext functionality with newly developed features such as graphical programming. In short, the TNC7 was developed to streamline everyday work at the machine.
Perfect design
The TNC7 will be the basis of future control generations from HEIDENHAIN. Beyond its unmistakable new look-and-feel, the control features high-quality hardware components and an advanced, individually adaptable user interface. Its entire operating concept was redesigned from the ground up. For all tasks, including programming, setup, and part measurement, the TNC7 provides optimal user support and maximum work flexibility with a rich packet of functions.
Individually adaptable user interface
The interface of the TNC7 was designed to help users achieve the best possible result with maximum speed and convenience. Different machining tasks call for individualized work environments, which is why users can adapt their screen content through personal favorites, their own home menu for a faster start, and more. As a result, all information and functions are exactly where they need to be. Based on data entry forms and dialog guidance, the user interface ensures optimal convenience and navigation aided by a smooth and precise touchscreen. And thanks to its fast operating speed, the control reacts immediately to data input. The keyboard was also redesigned for improved mechanics and optimized key resistance for greater comfort and reliability.
Smart programming
The TNC7 enhances familiar Klartext programming with smart functions and newly developed graphical programming. Users are able to draw contours directly on the touchscreen and convert them into dialog-guided TNC Klartext programming code. Cycles and older contour programs can still be used, including already existing NC programs. The TNC7 supports the entire manufacturing process from initial design to the finished part with carefully crafted solutions. These include a diverse package of functions, intelligent probing cycles, and graphical guidance for determining the position of clamping devices. A new, high-performance editor function enables fast and reliable editing of even complex NC programs. Perfect visualization of the machined part and work envelope make daily work easier, and programs can be simulated at any point without a change in operating mode.
Dynamic Collision Monitoring (DCM): the next generation
Users can enjoy complete machine protection thanks to the monitoring of machine elements, tools, and clamping devices. The TNC7 includes the next generation of Dynamic Collision Monitoring (DCM). Along with preventing collisions between machine components and tools, DCM now also accounts for clamping devices: the user can import 3D files of clamping devices and define their position with new graphical support. Collision protection is provided in both manual and automatic mode. Collisions can also be detected prior to machining with the control’s program test functionality. With it, the TNC7 realistically simulates the behavior of the workpiece, tool, and clamping device in high-resolution 3D graphics.
TNC Component Monitoring: protect the machine tool
TNC Component Monitoring is a toolbox allowing machine manufacturers to implement extensive monitoring functions. During machining, this function protects the spindle bearing from overloads, detects heightened component wear in the drive chain, and more. It also delivers valuable data about actual machine loads, letting users evaluate process capability and plan interventions as part of predictive maintenance. The TNC Component Monitoring function can also record and display the amount of wear on the recirculating ball screw or even warn users about spindle overloads.
TNC Process Monitoring: manufacture with reliability
The new, built-in TNC Process Monitoring function reliably detects process irregularities based on deviations from a reference machining run. The user controls this monitoring feature with Klartext syntax and an intuitive user interface. Process Monitoring requires no additional sensors and ensures dependable process quality. When combined with high-resolution sensors such as the ERM 6000 Dplus, Process Monitoring is even more effective for highly demanding applications. This enables the convenient control of process outcomes and maintains productivity thanks to a variety of configurable reactions, such as switching out a tool.
HEIDENHAIN at EMO Milano:
Oct. 4 – 9, 2021, Hall 7, Booth F05
Virtual EMO from HEIDENHAIN:
Live sessions on Oct. 11 – 29, 2021
www.heidenhain.com