www.ptreview.co.uk
14
'22
Written on Modified on
Intelligent solutions for demanding applications: encoders for every motion system at the HEIDENHAIN virtual trade show for automation
A virtual trade show for automation will exhibit new solutions for robotics, medical technology, elevators, and more from HEIDENHAIN and its brands AMO, ETEL, NUMERIK JENA, RENCO, and RSF. Discover ultra-compact encoders and encoders with added functionality, offering numerous benefits especially in low-space applications.
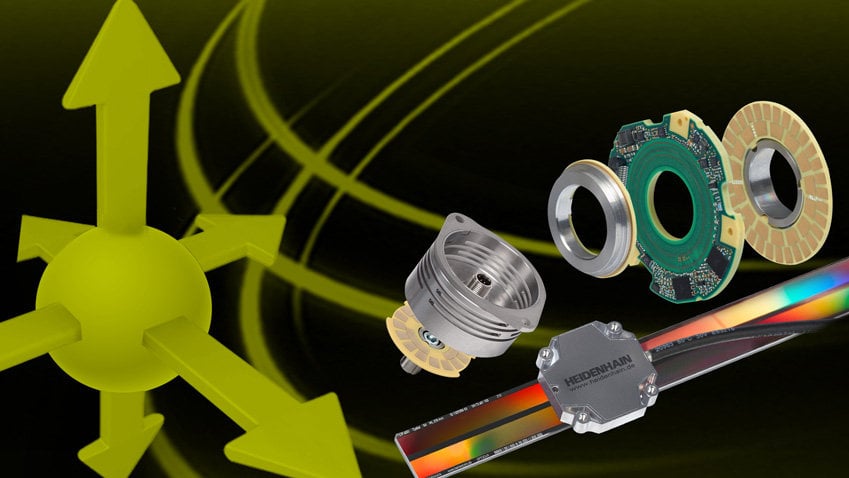
HEIDENHAIN KCI 120 Dplus: new possibilities for advanced robotics
The HEIDENHAIN KCI 120plus compensates for design-related positioning errors in dynamic, agile robots by combining motor feedback and position measurement in a single rotary encoder. This dual functionality is achieved with a single scanning unit and two circular scales in a compact, easily integrated design. This year’s automation virtual trade show will introduce the second generation of the KCI 120 Dplus, featuring an improved form factor. This version is smaller and accommodates a wider hollow shaft while offering the same functionality. Together, these two models cover a broad spectrum of applications, up to and including high-accuracy machining tasks. Thanks to their functionally safe EnDat 2.2 serial interface, they can even be used in safety-critical applications, such as cobots.
HEIDENHAIN KCI/KBI 1300 and KCI/KBI 100: small and light for compact servomotors
The KCI 1300 (singleturn) and KBI 1300 (multiturn) inductive rotary encoders with a 25 mm hollow shaft are designed for the compact motors used in robots and other applications. Their minimalistic design requires only a scanning unit and a single, screw-on circular scale or a press-fit disk/hub assembly. Along with their low profile and low weight, these encoders are immune to contamination and magnetic fields. Safety-critical installation is simple thanks to wide mounting tolerances and the functionally safe EnDat 2.2 interface. Operational reliability can be enhanced by an external temperature sensor for overload protection. New additions to the family, the KCI 100 and KBI 100, feature identical performance in a 30 mm or 40 mm hollow shaft.
AMO WMRA: secondary encoder for wide shaft diameters
Robotics engineers can vastly improve axis position accuracy by deploying a second, high-accuracy angle encoder. This secondary encoder is installed downstream from the gearbox, where it measures the actual position of each robot joint. The WMRA angle encoder from AMO is ideal for the job. Its design accommodates large shaft diameters and tight installation spaces thanks to its modular approach using a scanning unit and scale drum or a scanning unit and a measuring ring selectable in any diameter.
HEIDENHAIN ECI 1119 PressFit and EQI 1131 PressFit:
New inductive rotary encoders for automated installation onto compact motors
The new ECI 1119 PressFit (singleturn) and EQI 1131 PressFit (multiturn) absolute rotary encoders from HEIDENHAIN are the ideal solution for fast, easy, and reliable installation: these new encoders are suitable for small motors with a flange size of 40 mm x 40 mm and an axis height of 20 mm. Mounting is performed with a tolerance sleeve inserted into a circular opening in the motor housing. The encoder, with its PressFit flange, is pressed into the opening to create a friction fit and then fastened to the motor shaft with a central screw. This method saves space and enables automated assembly, a process that can be monitored via force measurement.
HEIDENHAIN KCI 419 Dplus: the rotary encoder for advanced elevators
The microswitches used for elevator brake monitoring are rendered obsolete by the KCI 419 Dplus elevator encoder. Beyond providing motor feedback, this encoder can be connected to the brake’s armature plate in order to detect the brake stroke. The resulting data allows the downstream electronics to determine the brake status (released or engaged) and the level of wear. Due to its proximity to the motor and brake, the KCI 419 Dplus can also provide valuable temperature monitoring data for analyzing malfunctions without the need for extra sensors. Because all of these parameters are transmitted by the purely digital EnDat 2.2 interface over a single cable, overall system cabling is greatly simplified. Further benefits include improved remote monitoring and predictive maintenance. In sum, the KCI 419 Dplus delivers greater elevator availability and reliability while reducing effort for installation, cabling, adjustment, and maintenance.
MULTI-DOF TECHNOLOGY from HEIDENHAIN: measure up to six degrees of freedom
Encoders such as the LIP 6000 Dplus or the GAP 1081 achieve much higher accuracy than usual by measuring motion in multiple degrees of freedom. Their MULTI-DOF TECHNOLOGY detects and compensates for deviations in additional directions of motion that negatively impact the overall system. The LIP 6000 Dplus contains two separate measuring standards on a single graduation carrier. One set of graduations is angled at +45° and the other at –45°. When scanned by a high-accuracy, two-field scanning head, the X and Y directions are measured simultaneously. Thanks to the EnDat 3 interface, these two position values are then sent to the control over a single cable, thus reducing installation effort and optimizing the system’s dynamic performance.
The GAP 1081 is the first gap encoder from HEIDENHAIN. It measures the vertical separation between a special mirror and the scanning head. When used alone, it is ideal for simple vertical positioning applications. When combined with a parallel-mounted linear encoder, such as the LIP 6000 Dplus, it can measure vertical deviations during linear travel. Mirrors for the GAP 1081 are available in lengths of up to 3 m. If two scanning heads are used on the same mirror, then the pitch and yaw can be measured.
Motor and positioning technology from ETEL: live motion system demonstrations
Visitors at the virtual trade show for automation can discover motor and positioning technology from ETEL. With its linear motors, torque motors, and AccurET controller, ETEL offers direct drive solutions for nanometer-level motion control and high-torque systems for industrial applications. The key benefits of these high-end motion systems from ETEL are their cogging-free design, optimum speed stability, and high control quality. When combined with high-accuracy HEIDENHAIN encoders such as in the CHARON2 from ETEL, they provide exceptional bidirectional repeatability and high dynamic performance for motion systems.
For critical applications big and small:
Convenient, accurate, and safe encoders for medical technology
With a proven track record in medical technology applications, encoders from HEIDENHAIN and its brands AMO, NUMERIK JENA, RENCO, and RSF are renowned for their reliability and fail-safe performance, making them ideal in highly specialized diagnostic, therapeutic, and lab solutions in hospitals and private practices. More than ever, the high accuracy of these rotary, angle, and linear encoders play a key role in patient comfort and application safety.
RENCO R35i / R35iL: the new rotary encoder generation for stepper and BLDC motors
In lab automation and liquid handling applications, the RENCO R35i and R35iL rotary encoders ensure high throughput and reliable operation. These incremental, bearingless solutions enable fast and accurate stepper and BLDC motor positioning on the many axes and belts used in blood-testing machines. With 40 000 measuring steps per revolution, they are the ideal motor feedback solution for these applications. If you need an encoder for the tight installation spaces of dialysis machines, blood pumps, and metering pumps, the RENCO R35iL features a profile height of just 8.6 mm, making it one of the flattest rotary encoders currently on the market. Installing the R35iL and R35i rotary encoders is easy even under challenging space constraints thanks to a user-friendly, self-centering mechanism for fast and precise alignment on the motor shaft. After installation, you can verify proper installation with the the PWT 101 testing device and its integrated traffic-light mounting assistant.
Measurement systems from AMO: new design possibilities for large medical equipment
Considering the high investment required for large medical equipment, reliable long-term operation is essential. System solutions from AMO are the ideal choice due to their touchless and wear-free inductive measuring principle, featuring insensitivity to contamination and high immunity to magnetic fields. Versions are available for linear and rotary axes, including for long measuring distances. For applications such as CT scanners, AMO measuring systems are available with incremental or absolute scanning in customer-defined diameters of up to several meters. Special solutions are available for use in high-energy radiation environments. The system’s measuring standard can be configured for either radial scanning or axial scanning: the scanning head is mounted on the inside or outside of the circular axis for radial scanning or laterally for axial scanning. Design engineers benefit from these unparalleled configuration options.
HEIDENHAIN LIC 4100: fast and jerk-free positioning for high-content screening
The LIC 4100 linear encoder from HEIDENHAIN is ideal for linear-axis applications requiring measuring steps at the nanometer level and high dynamic performance for maximum throughput. These encoders lay the foundation for fast, jerk-free resolution and high-detail imaging for correct and reliable results in highly automated microscopy applications such as in vitro diagnostics and high-content screening. The absolute measurement of the LIC 4100 delivers the position value immediately after switch-on, with no reference run needed. This ensures high process reliability in long, complex automated analysis runs. Reliability is further enhanced by the encoder’s built-in HEIDENHAIN Signal Processing ASIC (HSP 1.0), which eliminates the effects of contamination on the measuring standard. A functional safety option expands the encoders’ range of possible applications
www.heidenhain.com