Developers: Smart Sensors II – How Adding AI Can Predict the Future for IIoT
In many industrial settings, determining the current health of assets still involves a technician putting their ear to a machine to detect any ominous sound deviations. What they hear may indicate something has gone wrong, or worse, they hear silence, conveying that the equipment has completely failed. This is considered a reactive maintenance model.
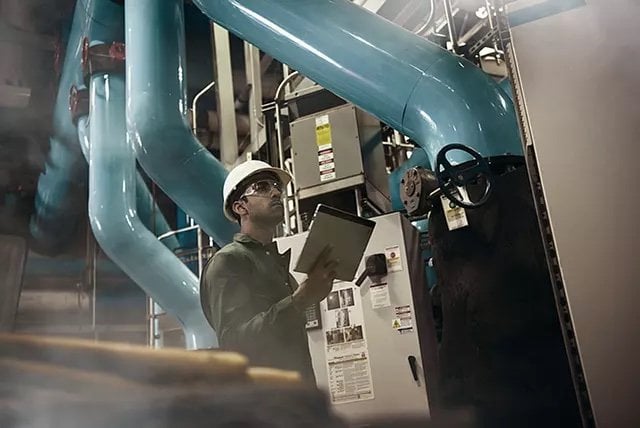
In our blog post, Building Smarter Edge Computing Solutions with Smart Sensors, we introduced the intelligence of smart sensors used to report on an asset's health and the utilization of threshold triggers for scheduled intervention. This is a preventive maintenance model.
This blog post looks at how a predictive maintenance model (PdM) comprising artificial intelligence (AI) at the edge within smart sensors, combined with advanced analytics, provides a way to evaluate an asset’s health through a prognostic lens.
Each of these maintenance models has a different impact on asset uptime and overall equipment effectiveness (OEE), as shown below:
Why is PdM important?
PdM helps to prevent unplanned reactive maintenance and avoids overdoing preventive maintenance. PdM allows maintenance frequency schedules to be super-efficient, and the insights provide value to an operation by:
- minimizing the number of unexpected breakdowns to improve reliability;
- maximizing production hours while improving safety; and
- streamlining operational and maintenance costs.
How Did We Get Here?
Various technologies have converged to make PdM possible – ML models, smart sensors, and advancements in connectivity.
Maintenance Models
ML Models – The sheer volume and velocity of data from industrial equipment make meaningful analysis a non-trivial task. However, by leveraging historical and real-time data, ML models can be trained to:
- detect anomalies by identifying unusual behaviors or patterns in machine components;
- predict machine failures before they cause downtime; and
- predict the remaining useful life (RUL) of components and systems.
Smart Sensors – Advancements in smart sensors are also expanding the capabilities of PdM. For example, sensors with onboard vector processing (e.g., Qualcomm Adreno GPU and Qualcomm Hexagon DSP found on our Snapdragon SoCs) can be used for computer vision inference during visual inspections to uncover hidden defects. In this case, external irregularities may indicate a more severe defect inside the sensor that should be reviewed.
Connectivity – Smart sensor SoCs now can include a range of connectivity options, including LPWA, LoRa, and NB-IoT. These advancements in connectivity make it possible to use real-time data to create dynamic digital replicas of physical entities called Digital Twins. By testing virtually before implementation, these replicas are invaluable in making model-driven decisions for prognostics.
Benefits and Examples of PdM in Action
By analyzing the past to predict the future, PdM can help reduce cost, increase productivity, increase lifespan, and improve safety in use cases such as these:
- Detecting Anomalies – for visual inspections of an aircraft fuselage, GPUs or specialized DSPs (e.g., Hexagon) excel at the vector processing required for image classification-based analytics to identify cracks. Identifying such irregularities may indicate a more severe defect inside that should be further investigated.
- Predict Machine Failures – focusing on a single asset is challenging in noisy factory environments. Deep learning and DSPs use noise reduction algorithms to perform vibration analysis. This analysis can identify and predict individual asset failure.
- Estimate Remaining Useful Life (RUL) – for remote equipment with multiple critical parts (such as wind turbines), features like edge connectivity and sensor fusion provides threshold analysis to determine the unit’s RUL.
Our Qualcomm Advantage Network Members are Making PdM Easier Than Ever
Implementing PdM from scratch can be a challenge, but developers today have the option to utilize “data science in a box” with automated PdM software. Qualcomm Advantage Network member Qeexo, are the makers of AutoML, a fully-automated, end-to-end machine learning (ML) platform. Their Detecting Anomalies in Machine Data blog post describes how to build an ML model for anomaly detection on machine vibration data.
Conclusion
Unplanned downtime costs industrial manufacturers a staggering $50 billion each year, and maintenance expenses make up 15% to 40% of total production costs. These statistics corroborate why PdM is one of the most discussed topics in the age of Industry 4.0, and why smart building technologies are ready for innovative solutions from IIoT developers.
Ready to implement PdM? Our application processors are designed to be embedded into a variety of IoT and edge use cases. Check out which application processor is right for you to see some of our solutions. We also have several tools and resources that can be used with our IoT solutions that feature the building blocks found in our Snapdragon SoCs, like:
- Qualcomm Neural Processing SDK is engineered to help you save time and effort in optimizing the performance of your trained neural networks.
- Qualcomm Computer Vision SDK allows you to add new user experiences into camera-based apps and includes a sample app to help kick-start your development.
- Qualcomm Machine Vision SDK is engineered to supply cutting-edge computer vision algorithms.
- AI Model Efficiency Toolkit (AIMET) provides a simple library plugin that AI developers can use to incorporate breakthrough model efficiency performance. The project is open-source on GitHub to facilitate collaboration between leading AI researchers.
For additional resources, check out our AI at the Device Edge Developer’s Guide. And if you are looking to combine 5G knowhow with IoT, industrial use cases, and edge computing, this announcement of our new processors and platforms for IoT industries will be of interest.
www.qualcomm.com