www.ptreview.co.uk
15
'24
Written on Modified on
Rolling bearing solutions and services for an optimized process chain in food production
Radial insert ball bearing and housing units made of plastic and monorail guidance systems specifically optimized for the food industry.
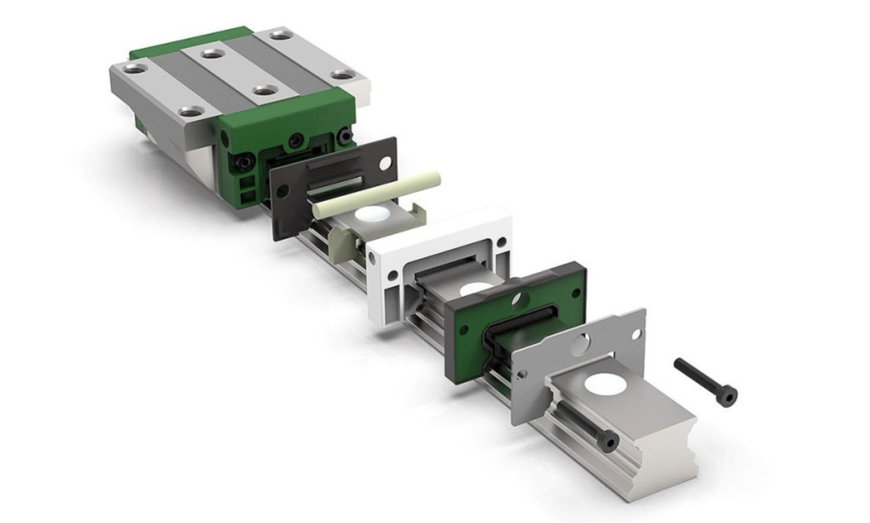
Anuga FoodTec is a must-attend event for the suppliers of machinery and equipment to the food industry. Around 1,700 exhibitors, more than 60 percent of them from abroad, will be exhibiting in Cologne. At Anuga FoodTec 2024, Schaeffler is presenting its latest products and services for the entire process chain in the food industry for the first time – from the processing and packaging of food through to the monitoring of entire production lines – and always with a focus on the conservation of resources and the reduction of operating costs and downtimes.
Radial insert ball bearing and housing units specifically for the food industry
Radial insert ball bearing and housing units are often used where conveyor belts and transport rollers are required. Schaeffler also offers these widely used machine components as a FOOD series (FD version). In addition to the corrosion-resistant bearings with food-grade lubricant, the housings of this RIBB..FD series are made from white plastic.
Linear guidance systems with lubrication and seal assembly for the food industry
Monorail guidance systems are used in a large number of linear motions during the processing and packaging of food, e.g. the series-KUVE..B four-row linear recirculating ball bearing and guideway assembly from Schaeffler. For all sizes of this series, Schaeffler offers an optimized lubrication and seal assembly specifically for the food industry. It comprises a KIT450 long-term lubrication unit, additional double lip wipers, non-contact sheet metal wipers, and food-grade flowable grease. Customers benefit from the reduced cleaning outlay for their machines, significantly longer relubrication intervals, and the option of changing over to lifetime lubrication in many cases.
Electric cylinders for harsh environments and low temperatures
Electric cylinders are widely used in food processing as adjustment drives and for actuating flaps, sliders, and sealing elements. For very stringent hygiene requirements, Schaeffler also offers series-CASM electric cylinders in a stainless steel version. Many cylinders and actuators are not in direct contact with food, for example, when they are used for redirecting and sorting on conveyor lines.
Schaeffler offers a large selection of electric cylinders of series CASM-25, -32, -40, -63, and -100 for these tasks. CASM IP54S electric cylinders are particularly suitable for applications in wet and dusty environments.
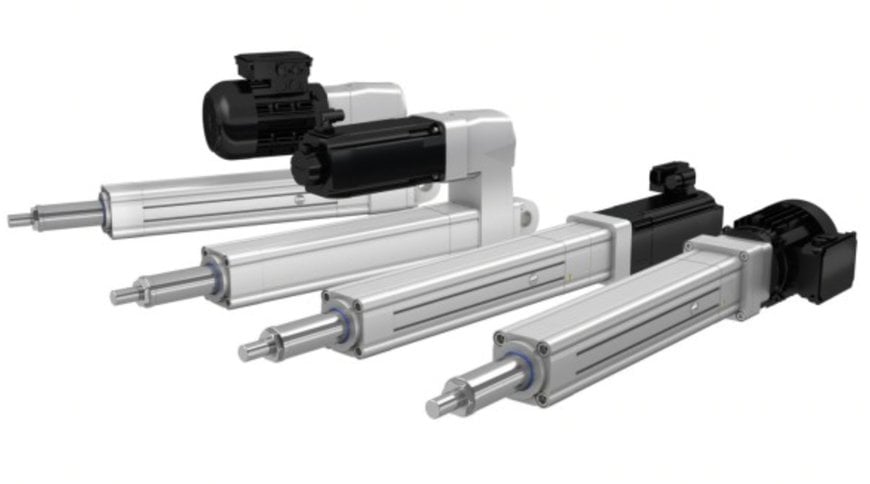
CASM-100 electric cylinders are equipped with asynchronous or synchronous motors and optionally with gearboxes with spur gears or a toothed belt and an intermediate flange. Ball and roller screw drives are used as linear drives.
Dynamic kinematics with precision gearboxes
The high throughput of food processing machines requires lightning-fast, fully-automated pick-and-place-solutions when handling and packaging. The challenge here is to implement multi-axis systems with standard components if possible. For rotary motion, Schaeffler offers RT1 and RT2-series precision strain wave gears and PSC-series precision planetary gearboxes. These are designed for demanding automation solutions and can also be supplied specifically configured for the customer as a complete drive with drive motors.
Relubrication and condition monitoring
The OPTIME C1 lubricator is an innovative and intelligent lubrication solution. The C1 lubricator and OPTIME vibration sensors connect to each other and the gateway autonomously to form a mesh network and are configured and ready for operation in just a few minutes. With the OPTIME mobile app, the maintenance team has an overview of the condition of all machines, such as pumps, mills, fans, gearbox motors and units, and every lubricator of type OPTIME C1. Apart from the savings in terms of inspections and manual measurements, the OPTIME ecosystem reduces expensive, unplanned production stoppages, which, in turn, increases the annual production volume.
www.schaeffler.com