www.ptreview.co.uk
10
'24
Written on Modified on
Raising the bar for tomorrow’s standards
By Bradley McEwan, business development manager at automation and control technology specialist Beckhoff UK, discusses how software and modular hardware enables easy integration of technologies, like robotics and vision, that were once considered 'standalone'.
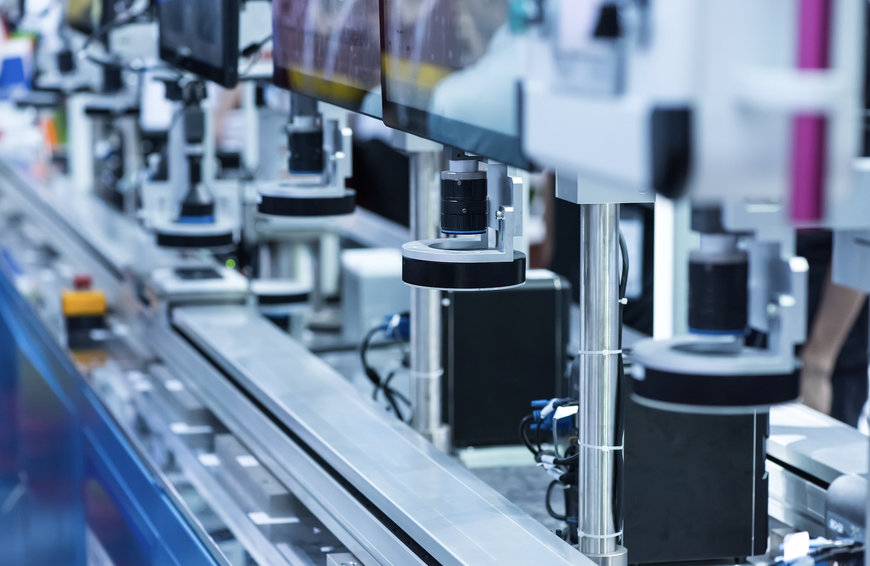
The markets are changing, and thus so are the requirements of the process manufacturing industry. Whether it is fluctuating demand, more customised products or smaller batches, manufacturers need to respond more quickly and flexibly.
Flexible manufacturing is a modern approach that emphasises adaptability, responsiveness and customisation in the production process. Unlike traditional mass production, where the focus is on producing large quantities of identical products, flexible manufacturing systems can efficiently handle small to medium-sized production runs and easily adapt to changes in product design or customer requirements.
Enabling manufacturers to quickly switch between different products without incurring significant downtime or retooling costs, the move towards flexible manufacturing happened before the destruction of the supply chain, pandemic and global wars. In fact, a major driving force behind the move was because of short run times and manufacturers wanting to test the market with products, owing to end users promoting seasonal events, such as Easter and Christmas.
Machine life cycles
Typical commercial products, such as shampoo, used to have a life cycle of between three and five years. Therefore, it was financially viable for manufacturers to buy machinery solely for a single product that has a long-life cycle.
Now, we are now seeing a significant decrease in the life cycle of commercial products, which is paving the way for flexible manufacturing. Manufacturers are no longer tied to a product line for the same amount of time, instead they require a production line that consists of at least two or three products.
The advent of Industry 4.0 kickstarted the need for machines to become smart integrating into the ‘cloud’ for data analysis to enable seamless reconfiguration. As a result, this changed how manufacturing companies evaluated the capital investment of machines, as the emphasis switched from being on the life cycle of the product, to the life cycle of a machine.
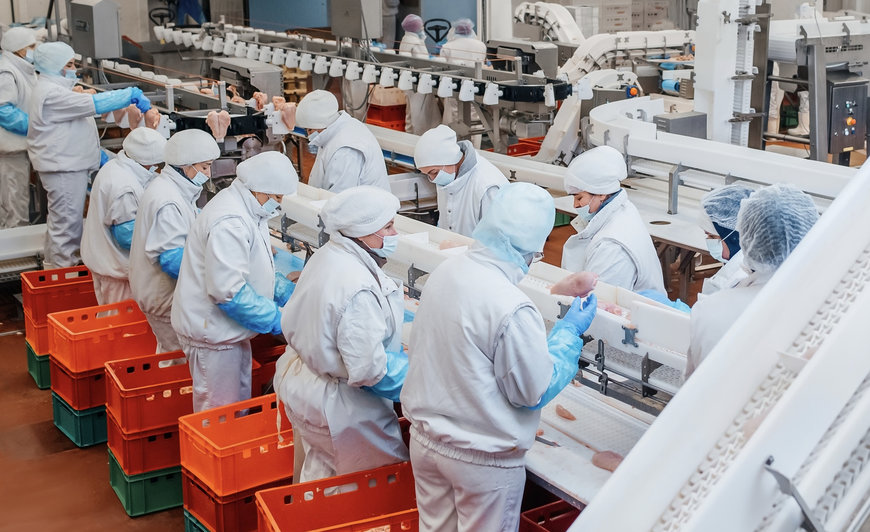
After all, it is not financially viable to buy new machinery every 18 months. Not only it is a significant upfront cost, but it also takes around two years to get the machine sealed and delivered ready for use.
Variable product flow
Traditionally, a production line would have a continuous flow of product, often referred to as a continuous production process or continuous flow manufacturing. This approach is characterised by the steady and uninterrupted movement of products along the production line, with each station performing a specific operation in a sequential manner.
Yet, the introduction of flexible track systems is enabling production lines to have a variable flow of product. Flexible track systems consist of modular units that can be easily connected or rearranged to form different production lines or workstations, ensuring quick reconfiguration to accommodate various product types or changes in production requirements.
These systems, such as Beckhoff’s TwinCAT software platform, combine the advantages of flexible manufacturing with the efficiency of continuous production, achieving greater adaptability and responsiveness to changing demands while maintaining high throughput and efficiency.
Laying down the foundation for modular production, the TwinCAT software-based approach integrates Programmable Logic Controller (PLC), motion control, robotics, vision, Human-Machine Interface (HMI), cloud connectivity and other functionalities into a single software environment. And, as Industrial PCs (IPCs) increase in power, the TwinCAT platform allows for further integration.
By reducing the number of components, such software is designed to allow original equipment manufacturers (OEMs) to enable modular production and start their flexible manufacturing process. In fact, we believe that PC based automation is a move away from the traditional fixed PLCs, enabling the easy integration of robotics, vision and machine learning applications that were once unimaginable.
www.beckhoff.com