www.ptreview.co.uk
11
'25
Written on Modified on
Voith & DLR Advance AI Turbine Design
Voith and DLR are achieving initial successes in AI-driven turbine development, using AutoOpti for advanced optimization to significantly boost efficiency and shorten design times.
voith.com
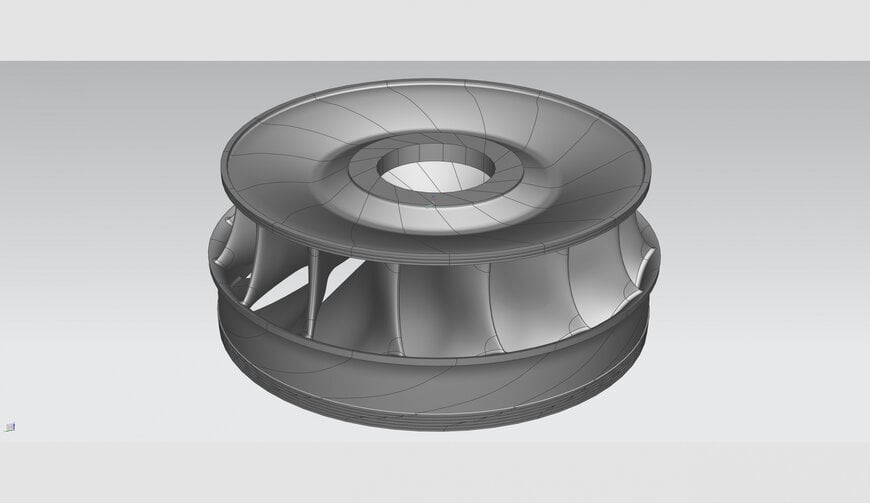
In a pioneering collaboration project, Voith, one of the leading manufacturers of hydropower plants, and the DLR Institute of Propulsion Technology are combining their expertise to improve the design process of water turbines through advanced, AI-assisted optimization methods. The goal of this cooperation is to fundamentally enhance turbine development by using intelligent optimization techniques. To achieve this, the engineers are establishing a multidisciplinary optimization system that significantly boosts turbomachinery efficiency while deepening the physical understanding of complex flow phenomena.
Hydropower is one of the key pillars of sustainable energy supply. At the same time, modern water turbines face increasing innovation pressure. Energy providers and plant operators now expect maximum efficiency, long service life, and high operational safety under increasingly strict economic and regulatory conditions. One of the biggest challenges in development is the design of complex flow components such as runners and guide vanes. Simultaneously, digitalized, data-driven processes are becoming more important, which is essential for remaining competitive in the global market. On top of that, development time and costs are under more scrutiny than ever. To meet these demands, new approaches to turbine design are required.
The DLR tool AutoOpti: optimization for complex turbine systems
At the heart of the project is the optimization tool AutoOpti, developed by DLR. This software was specifically created for automated, interdisciplinary design processes and optimization. AutoOpti allows the integration of fluid dynamics, structural mechanics, and other simulation models, incorporating intelligent strategies for design selection and model reduction.
In cooperation with Voith, AutoOpti is being used specifically for flow-mechanical optimization of turbine components. In practice, this means turbine components such as rotors or guide vanes can be adjusted in a targeted way to minimize hydraulic losses and reduce mechanical stress, much faster than with conventional development approaches.
How machine learning methods are advancing turbine development
In this innovation project, real geometries and boundary conditions from Voith’s product development are incorporated into an automated optimization process. AutoOpti takes full control: it generates new designs, automatically runs simulations, and evaluates results based on target criteria such as hydraulic efficiency, flow losses, or mechanical robustness. With the help of established surrogate models (Gaussian Processes), the number of costly CFD calculations required is significantly reduced. This combination allows the design space to be systematically and efficiently explored.
Initial results: efficiency gains become apparent
Even in the early stages of the project, the potential is clear: In the optimization of a Francis turbine, AutoOpti was able to generate new design variants that achieved significant efficiency improvements at multiple operating points—while maintaining constant flow rates. In parallel, initial surrogate models were successfully trained using high-fidelity CFD data and effectively integrated into the optimization process. The results so far confirm: AutoOpti significantly shortens development time while measurably improving the quality of turbine design.
Outlook: scaling and further development
The next step is to expand AutoOpti’s application to additional turbine components and to integrate further physical disciplines. Additionally, the potential to apply AutoOpti optimization to other Voith product lines is being evaluated.
The DLR Institute of Propulsion Technology is closely supporting this process—through technical workshops, tailored training, and ongoing assistance in integrating these methods into existing development workflows. In the long term, the aim is to transform this successful cooperation into a lasting development partnership.
In addition to traditional machine learning methods used in AutoOpti (e.g., Gaussian Processes), the Institute of Propulsion Technology is currently developing new deep neural network approaches (DNNs) with FlowFormer, based on transformer architectures that directly approximate 3D flow behavior.
www.voith.com