www.ptreview.co.uk
16
'25
Written on Modified on
WAGO expands successful collaboration with Jungheinrich
Fully automated small load carrier supply in tight spaces transports six carriers simultaneously, easing employee workload and ensuring future viability with VDA 5050-compatible solution.
www.jungheinrich.co.uk
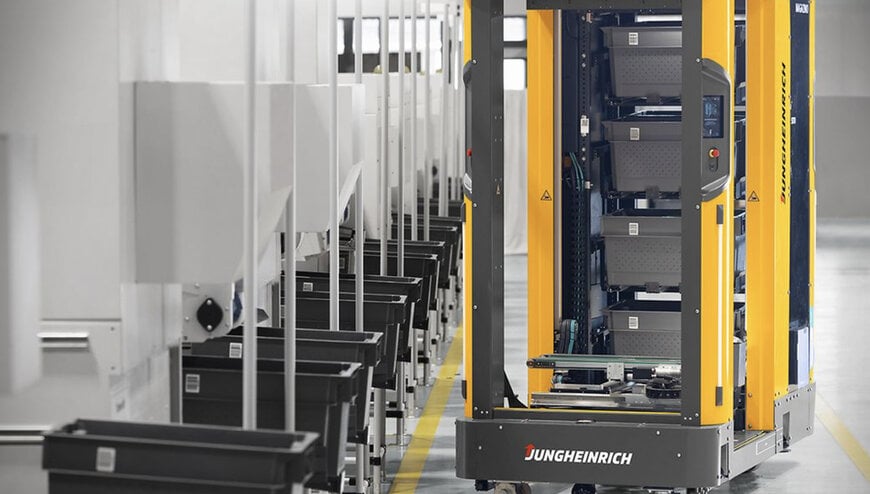
Following a demonstration project that has been successfully in operation since 2023, WAGO GmbH & Co. KG has decided to scale up its mobile robot solution. In the future, a total of four SOTO robots from Jungheinrich subsidiary Magazino will take over the fully automated supply and disposal of injection moulding machines with small load carriers in three-shift operation.
Innovative technology successfully scaled
The deployment of a SOTO robot, which was launched as a pilot project in 2023, impressed WAGO with its efficiency and flexibility in the production environment. The mobile robots transport empty small load carriers to the production machines and transport finished parts from production to the logistics area. “SOTO has proven itself to be a future-proof solution for our production supply,” explains Thorben Eppmann, Technical Process Engineer at WAGO. “Following the positive experience with SOTO during the demonstration operations, we are moving forward with a fleet expansion. In the future, our employees will be relieved of physically demanding work to an even greater extent, allowing them to concentrate fully on value-adding activities.”
Maximum efficiency due to intelligent multiple transports
The SOTO robots impress with their unique ability to transport several small load carriers at the same time. This drastically reduces vehicle traffic in the production area and at the same time increases supply security. The omnidirectional drive technology allows precise manoeuvring, even in spaces that are only 1.65 metres wide. This is a decisive advantage in the tight machine park.
The autonomous navigation requires no artificial landmarks. SOTO orients itself independently based on the space’s contours using four laser scanners and two 3D cameras. The robot navigates its way independently and reliably along authorised routes while the 360°-degree sensors recognise unexpected people and objects. If there is imminent danger, it stops immediately. At the same time, the maintenance-free lithium-ion technology with automatic interim charging enables uninterrupted 24/7 operation.
Future-proof system architecture
The fleet is fully VDA 5050 compatible and is coordinated via a master control system that is not dependent on any single manufacturer. This standardised interface ensures maximum flexibility and expandability.
A customised conveyor technology concept in the logistics area and a customer-specific rack design on the injection moulding machines are the transfer points for the SOTO robots. This ensures optimum decoupling between production and logistics.
“This successful scaling proves the enormous potential of mobile robots for German industry,” emphasizes Magazino Sales Manager Paul Seluga. “By expanding its automation solution, WAGO is increasing the efficiency of its internal logistics and creating room for further growth,” adds his colleague Janik Brinmühl, Project Manager for Intralogistics Systems at Jungheinrich.
www.jungheinrich.com