www.ptreview.co.uk
27
'24
Written on Modified on
Three steps to reduce CNC machining waste
By Hakan Aydogdu, general manager at CNC automation manufacturer, Tezmaksan Robot Technologies outlines three steps manufacturers can take to avoid wasting machine shop resources.
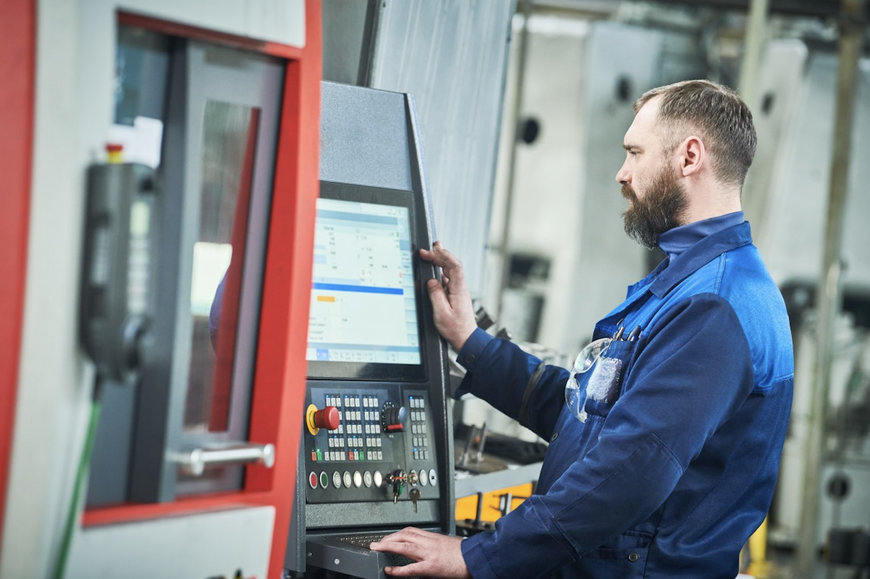
Sustainability is a key concern in CNC machining, with manufacturers grappling to minimise material waste and maximise machine efficiency, while maintaining profitability.
Going circular
Material waste remains pervasive in machining but, recycling rates for metals are far lower than their potential for reuse. In fact, according to a UN Environment Programme (UNEP) Status report, less than one third of metals currently have a recycling rate above 50 per cent.
As the world strives to confront climate change in a race against time, organisations like UNEP advocate for the adoption of circularity. In most machine shops this means re-using materials from products that have been recycled and re-using, repairing and recycling components wherever possible. Circularity is certainly no stranger in the metal cutting world, but not all machine shop owners are applying this methodology.
Different materials will cause different shearings as well as creating carving residue and debris that will be produced during cutting. Steel, aluminium, brass and copper are all widely recycled, and carbide cutting tools can often be returned to machine tool manufacturers for recycling too.
Manufacturers can reuse some of the material waste and scrap for other projects, such as prototypes, test parts or accessories. Furthermore, making new tools from recycled materials requires less energy and emits less carbon dioxide, making production more sustainable and cost-effective. In large machine shops, a dedicated circulatory contact could be viable, while smaller organisations should invest in research and training.
Optimising processes for efficiency
Modern CNC machining can achieve a high degree of reproducibility, improving repeatability and processes, which has a direct impact on the conservation of resources. One of the most effective ways to manage material waste and scrap is to carefully plan the product’s design.
Inserts with consistent performance avoid workpiece damage, which minimises workpiece material waste. If CNC operators optimise part geometry, nesting and tool paths using the most appropriate material size and shape for their project, they can avoid waste material.
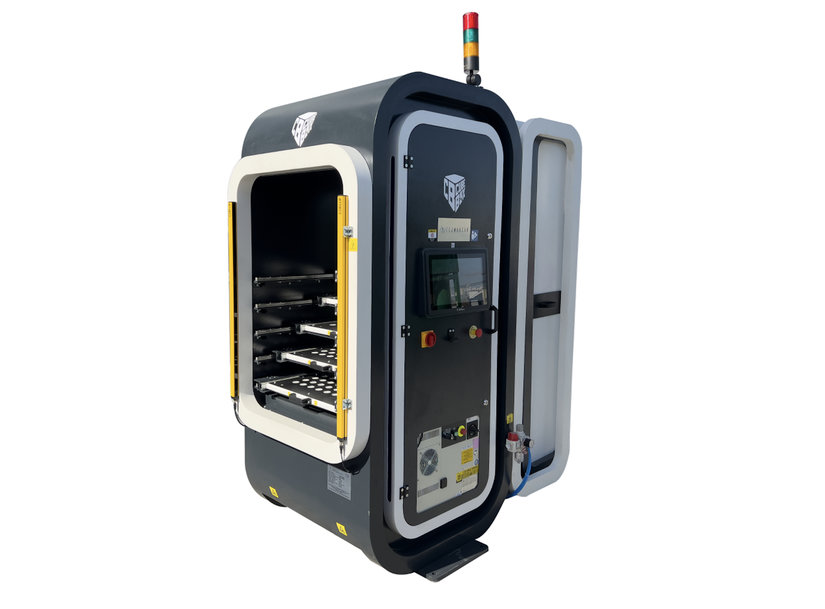
An alternative approach to waste reduction involves controlling the rhythm of production. Manufacturers can take care of equipment to make it last longer by decreasing cutting speeds depending on the material they’re working with. This simple change can sustain their productivity by raising the feed rate and depth of cut, which not only conserves energy but also extends the lifespan of tools that contain metals such as aluminium, brass, copper, steel, or titanium.
Connecting equipment
To work effectively with other machines and maximise the benefits of a smart factory, each CNC grinding machine will need to be connected to a communication network. This way operators can analyse material usage, monitor and measure waste, so plant managers can identify the causes of waste and implement corrective actions to conserve resources.
Robotic automation systems are designed to enhance manufacturing processes and reduce operator involvement in machine tending, increasing productivity and reducing downtime. For example, Tezmaksan’s CubeBOX system enables manufacturers to operate robotic systems without the need for specialised programming knowledge.
This technology is able to convert 2D CAD drawings into CAM instructions thanks to its RoboCAM software, simplifying the entire process. It is compatible with all CNC machines, including all types of CNC lathes, machining centres and grinding machines. The CubeBOX system allows multiple machines to operate seamlessly without interruptions caused by loading and unloading, providing continuous service without operators, which translates to 50 per cent enhancement in nocturnal shift efficiency.
The combination of circular economy methodologies, monitoring performance and connecting equipment addresses global sustainability challenges while taking care of waste. To stay competitive in the ever-evolving industrial automated landscape, manufacturers need to rely on specialised robotic systems to improve processes and take their business to the next level.
For more information.
www.tezmaksan.com